【佛山市德龍信環保設備有限公司】秉承創新發展的理念,緊跟時代步伐,致力于新質生產力與智能智造技術的研究與開發。公司專注于污水處理設備的研發和生產,同時,也在低碳環保材料領域不斷探索,旨在為中小企業提供更加先進、節能、高效的環保產品。在追求環保與可持續發展的今天,德龍信環保設備有限公司深知責任重大。以下是關于公司發展理念:
首先,公司緊跟科技發展的前沿,不斷研發新技術,推動污水處理設備向智能化、自動化方向發展。通過引入先進的控制系統,不僅提升了設備的處理效率,還大大降低了能耗,為中小企業帶來了顯著的成本效益。
其次,德龍信環保設備有限公司注重產品的環保性能,采用低碳環保材料,減少生產過程中的碳排放。這些環保材料的應用,既滿足了企業的生產需求,又為保護環境做出了積極貢獻。
最后,公司始終堅持以客戶為中心,深入了解中小企業的實際需求,提供定制化的解決方案。通過持續的技術創新和優質的售后服務,德龍信環保設備有限公司贏得了廣大客戶的信賴,成為環保行業中知名品牌企業。
【佛山市德龍信環保設備有限公司】脫硫廢水處理方法主要包括以下幾種,可針對廢水中的高鹽、重金屬等污染物進行去除:
化學沉淀法
? 原理:通過投加石灰、碳酸鈉等化學藥劑,使廢水中的重金屬離子(如鈣、鎂、銅等)形成氫氧化物或碳酸鹽沉淀,從而去除。
? 特點:操作簡單、成本較低,是最常用的預處理方法,但可能產生大量污泥。
蒸發結晶法
? 原理:對廢水進行加熱蒸發,使水分汽化,殘留的鹽分結晶析出,實現水與鹽的分離。
? 特點:可徹底去除鹽分,出水水質好,但能耗較高,適用于對水質要求高的場景。
膜處理法
? 原理:利用反滲透(RO)、納濾(NF)等膜技術,通過膜的截留作用去除廢水中的鹽分和污染物。
? 特點:處理效率高、占地小,但膜易受污染,需要定期清洗或更換,成本較高。
生物處理法
? 原理:利用微生物的代謝作用,降解廢水中的有機物,同時去除部分重金屬。
? 特點:環保、成本低,但處理周期長,對水質條件要求較高,通常作為輔助工藝。
電化學法
? 原理:通過電解作用,使廢水中的污染物發生氧化還原反應,生成沉淀或氣體去除。
? 特點:反應速度快、處理效果穩定,但能耗和設備成本較高。
實際應用中,常采用多種方法組合處理,例如“化學沉淀+蒸發結晶”或“膜處理+生物處理”,以達到更好的處理效果和經濟性。
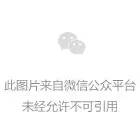
蒸發結晶法處理脫硫廢水的具體步驟如下,主要通過加熱蒸發和結晶分離實現污染物去除:
1. 預處理
? 去除懸浮物和重金屬:先通過化學沉淀法(投加石灰、碳酸鈉等)去除廢水中的懸浮物及大部分重金屬離子,避免后續設備堵塞或結垢。
? 調節pH值:將廢水pH調至中性或弱堿性,減少對蒸發設備的腐蝕。
2. 蒸發濃縮
? 加熱蒸發:將預處理后的廢水送入蒸發器(如多效蒸發器、機械蒸汽再壓縮蒸發器MVR),通過加熱使水分汽化。
? 蒸汽循環利用:產生的二次蒸汽經冷凝后可作為回用水,提高熱效率、降低能耗(如MVR技術通過壓縮機回收蒸汽熱量)。
3. 結晶析出
? 濃縮液處理:當廢水濃縮到一定程度(鹽分濃度升高至過飽和),鹽分開始結晶析出。
? 結晶設備:通過結晶器(如強制循環結晶器)促進晶體生長,形成較大顆粒的鹽晶體(主要為氯化鈉、硫酸鈉等)。
4. 固液分離
? 離心或過濾:將結晶后的混合液送入離心機或過濾器,分離出鹽晶體和少量母液。
? 母液回流:母液中仍含少量鹽分,可回流至蒸發器再次處理,減少廢水排放。
5. 產品處理與出水回用
? 鹽晶體處理:分離出的鹽晶體經洗滌、干燥后,可作為工業鹽回收利用(需滿足相關標準),或按固廢處理。
? 冷凝水回用:蒸發產生的冷凝水水質較好,可回用于電廠循環水系統或作為脫硫工藝補水。
核心特點
? 優勢:可徹底去除鹽分,出水水質達標,適合零排放要求;鹽類可回收,減少固廢處理壓力。
? 不足:能耗較高(加熱需消耗蒸汽或電能),設備投資大,需定期清理蒸發器內的結垢問題。
實際應用中,常結合預處理工藝(如化學沉淀)提升效率,或采用MVR等節能技術降低能耗。
蒸發結晶法處理脫硫廢水的優缺點如下,其核心優勢在于鹽分去除徹底,不足則與能耗和成本相關:
優點
? 鹽分去除徹底:通過蒸發濃縮和結晶,可將廢水中的鹽分(如氯化鈉、硫酸鈉)完全分離,實現“零排放”目標,出水水質滿足回用要求(如作為循環水或工藝補水)。
? 回收利用價值高:分離出的鹽晶體(經處理后)可作為工業鹽回收,減少固廢處理成本,符合資源化利用理念。
? 處理效果穩定:工藝原理簡單,不受水質波動影響,對高鹽、高硬度廢水適應性強,適合長期連續運行。
? 操作自動化程度高:可搭配多效蒸發(MEE)、機械蒸汽再壓縮(MVR)等技術,實現系統自動化控制,減少人工干預。
缺點
? 能耗成本高:蒸發過程需持續加熱(如蒸汽、電能),尤其對于大水量廢水,能耗費用占比顯著(如MVR技術雖節能,但設備投資更高)。
? 設備投資與維護成本高:蒸發器、結晶器等設備材質需耐高鹽腐蝕(如鈦合金、不銹鋼),初期投資大;且長期運行易產生結垢,需定期清洗或更換部件,維護成本高。
? 污泥處理壓力大:預處理階段(化學沉淀)會產生大量污泥,若鹽晶體中混有重金屬,可能需按危險廢物處理,增加處置難度。
? 占地面積較大:多效蒸發等工藝需布置多個蒸發單元,對場地空間要求高,不適合小型處理場景。
總結
蒸發結晶法適用于對出水水質要求高、需實現零排放的場景(如大型電廠),但需結合節能技術(如MVR)和預處理工藝(減少結垢)降低成本。若廢水鹽分濃度較低或處理規模較小,可考慮與其他方法(如膜處理)結合使用,優化經濟性。
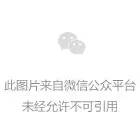
蒸發結晶法處理脫硫廢水的適用范圍主要基于水質特點、處理目標及場景需求,具體如下:
1. 水質條件適用范圍
? 高鹽廢水:適用于含鹽量較高的脫硫廢水(如總溶解固體TDS>10000 mg/L),尤其適合經預處理后仍含大量氯化鈉、硫酸鈉等可溶性鹽的廢水。
? 高硬度/重金屬廢水:可配合化學沉淀法先去除重金屬和鈣鎂離子,再通過蒸發結晶處理剩余鹽分,避免結垢影響蒸發效率。
2. 處理目標適用場景
? 零排放要求:當企業需實現廢水“零排放”(如環保政策嚴格地區、水資源匱乏區域),蒸發結晶法可徹底分離水分和鹽分,滿足嚴苛排放標準。
? 水資源回用:蒸發產生的冷凝水水質優良(TDS<100 mg/L),可回用于電廠循環水系統、脫硫工藝補水或鍋爐軟化水等,實現水資源循環利用。
? 鹽類資源化:若廢水中鹽分純度較高(如氯化鈉含量>90%),結晶分離的鹽晶體可經處理后作為工業鹽出售(需符合《工業鹽》GB/T 5462等標準),降低處理成本。
3. 行業與場景適用范圍
? 電力行業:燃煤電廠脫硫廢水因高鹽、高硬度特性,常采用蒸發結晶法實現零排放,尤其適用于大型電廠(處理水量大、有蒸汽資源可利用)。
? 化工/冶金行業:如煤化工、鋼鐵廠的脫硫廢水,若水質與電廠類似,也可采用此工藝。
? 工業園區集中處理:當多個企業廢水需集中處理時,蒸發結晶法適合作為終端處理工藝,統一實現鹽分去除和水回用。
4. 不適用場景
? 低鹽廢水:若廢水TDS<5000 mg/L,蒸發結晶的能耗成本較高,經濟性差,更適合膜處理等工藝。
? 小水量分散處理:小型企業或處理量<100 m3/d的場景,因設備投資占比高,不建議單獨使用蒸發結晶法,可考慮與其他工藝(如化學沉淀+膜過濾)組合。
? 含易揮發有毒物質廢水:若廢水中含氨、揮發性有機物(VOCs),蒸發過程中可能隨蒸汽逸出,需額外增加處理步驟,否則易造成二次污染。
總結
蒸發結晶法更適合處理量大、鹽濃度高、有零排放或資源化需求的脫硫廢水場景(如大型電廠、工業園區),但需結合水質預處理(防結垢)和節能技術(如MVR)優化成本。對于低鹽、小水量或成分復雜的廢水,建議優先選擇其他工藝或組合處理方案。影響蒸發結晶法處理脫硫廢水效果的因素主要涉及水質特性、工藝參數和設備運行等方面,具體如下:
1. 水質特性
? 含鹽量(TDS):
? TDS過高(如>50000 mg/L)會加速溶液過飽和,促進結晶,但可能增加設備結垢風險;TDS過低則蒸發能耗占比上升,經濟性下降。
? 鹽分組成:
? 硫酸鈉、氯化鈉等易結晶鹽類占比高時,結晶效率更高;若含硝酸鈉、氯化鈣等溶解度受溫度影響大的鹽,需調整蒸發溫度優化結晶效果。
? 重金屬與懸浮物:
? 預處理不徹底時,重金屬離子(如鈣、鎂)易與碳酸根、硫酸根形成沉淀,堵塞管道或在蒸發表面結垢;懸浮物過多會影響晶體純度,增加固液分離難度。
? pH值:
? 酸性條件下設備腐蝕加??;堿性條件下易生成碳酸鈣、氫氧化鎂等沉淀,導致結垢,通常需將pH調至6-8范圍。
2. 工藝參數
? 蒸發溫度與壓力:
? 溫度過高可能導致鹽分分解(如碳酸氫鹽),或加速設備結垢;負壓蒸發(減壓)可降低沸點,減少能耗,但需配套真空系統。
? 蒸發速率:
? 蒸發速率過快會導致晶體顆粒細小,增加固液分離難度;速率過慢則影響處理效率,需根據鹽分溶解度曲線調整(如氯化鈉溶解度受溫度影響小,可采用恒速蒸發)。
? 濃縮倍數:
? 濃縮倍數過高(如超過飽和濃度2倍)會導致大量細晶析出,堵塞管道;過低則結晶效率低,需平衡能耗與結晶效果(通常濃縮至TDS為初始值的3-5倍)。
3. 設備與操作
? 蒸發器類型:
? 多效蒸發器(MEE)能耗較低,但占地面積大;機械蒸汽再壓縮(MVR)節能性好,但對蒸汽壓縮機維護要求高,設備類型影響處理效率和能耗。
? 攪拌強度:
? 結晶器內攪拌不足會導致晶體分布不均,形成結壁;攪拌過強則可能打碎晶體,影響顆粒度(理想攪拌速度需使晶體懸浮但不破碎)。
? 結垢控制:
? 未定期清洗蒸發器表面時,鈣鎂鹽類結垢會降低傳熱效率(如傳熱系數下降50%以上),需通過加阻垢劑、定期酸洗(如檸檬酸)或超聲波除垢維持設備性能。
4. 預處理效果
? 若預處理未去除足夠的懸浮物和重金屬,蒸發過程中易形成“晶核”雜質,影響鹽晶體純度(如重金屬含量超標導致晶體無法回用),或加速設備結垢。
5. 運行穩定性
? 蒸汽供應波動(如壓力不穩)會導致蒸發溫度波動,影響結晶顆粒均勻性;頻繁啟停設備易造成晶體在管道內沉積,降低系統可靠性。
總結
優化蒸發結晶法效果需從水質預處理(除重金屬、懸浮物)、精準控制工藝參數(溫度、濃縮倍數)、選擇合適設備(如MVR降低能耗)及加強結垢維護入手,尤其需根據廢水鹽分特性調整蒸發策略,以平衡處理效率、能耗成本和晶體純度。蒸發結晶法處理脫硫廢水的具體操作步驟通常包括預處理、蒸發濃縮、結晶分離及后續處理,以下是詳細流程:
1. 預處理階段:去除雜質,優化水質
? 中和調節pH:
? 向廢水中投加石灰(Ca(OH)?)或氫氧化鈉(NaOH),將pH調至8-9,使重金屬離子(如Fe3?、Cu2?)生成氫氧化物沉淀,同時去除部分碳酸根、硫酸根離子。
? 化學沉淀除重金屬:
? 加入硫化鈉(Na?S)或有機硫藥劑,與殘留重金屬(如Hg2?、Pb2?)反應生成硫化物沉淀,通過混凝(加聚合氯化鋁PAC)和絮凝(聚丙烯酰胺PAM)強化固液分離,經沉淀池或過濾器去除懸浮物。
? 軟化除硬度:
? 投加碳酸鈉(Na?CO?)去除鈣離子(Ca2?),加氫氧化鈉去除鎂離子(Mg2?),生成碳酸鈣、氫氧化鎂沉淀,降低廢水硬度,防止蒸發過程結垢。
2. 蒸發濃縮階段:減少水量,提升鹽分濃度
? 多效蒸發(MEE)或機械蒸汽再壓縮(MVR):
? MEE流程:廢水進入多效蒸發器(如3-5效),利用前一效的二次蒸汽作為下一效的熱源,依次蒸發濃縮。例如,第一效通過生蒸汽加熱,產生的二次蒸汽進入第二效,以此類推,最終濃縮液TDS提升至30000-50000 mg/L。
? MVR流程:通過蒸汽壓縮機將蒸發產生的二次蒸汽壓縮升溫,重新作為熱源加熱廢水,形成閉式循環,能耗較MEE降低30%-50%。
? 控制蒸發參數:
? 保持蒸發溫度60-90℃(根據鹽分特性調整,如氯化鈉適宜70-80℃),負壓蒸發可降低沸點;控制蒸發速率避免結垢,定期監測濃縮液濃度,達到設定值后送入結晶器。
3. 結晶分離階段:析出鹽分,實現固液分離
? 結晶器操作:
? 濃縮液進入強制循環結晶器,通過攪拌(轉速50-100 rpm)使溶液保持均勻懸浮狀態,利用蒸發或冷卻使鹽分過飽和結晶。例如,氯化鈉采用蒸發結晶(溫度恒定),硫酸鈉采用冷卻結晶(降低溫度至30℃以下)。
? 固液分離:
? 結晶后的混合液經旋流器初步分離,粗晶體進入離心機或板框壓濾機脫水,得到含水率<10%的鹽餅;濾液返回蒸發系統繼續處理,冷凝水(TDS<100 mg/L)經pH回調后回用。
4. 后續處理:冷凝水回用與鹽餅處置
? 冷凝水回用:
? 冷凝水經活性炭吸附或精密過濾去除微量有機物后,回用于電廠循環水系統、脫硫工藝補水或鍋爐軟化水預處理單元。
? 鹽餅處理與資源化:
? 若鹽餅純度高(NaCl>90%),經洗滌、干燥后可作為工業鹽出售(需符合GB/T 5462標準);若含重金屬(如Hg、As),需按危險廢物鑒定標準(GB 5085.3)判定,合規后送危廢填埋場或固化處理。
5. 輔助系統:結垢與腐蝕控制
? 結垢預防:
? 向蒸發器中投加有機膦系阻垢劑(如ATMP),抑制碳酸鈣、硫酸鈣結晶;定期用檸檬酸(濃度2-3%)循環清洗換熱表面,去除結垢層。
? 設備防腐:
? 蒸發器主體采用鈦合金(TA2)、316L不銹鋼或襯膠材質,管道連接處使用氟橡膠密封,減少高鹽、高pH環境下的腐蝕。
操作要點總結
? 預處理需徹底去除重金屬和硬度,避免蒸發結垢及晶體污染;
? 根據鹽分特性選擇蒸發工藝(MEE/MVR)和結晶方式(蒸發/冷卻);
? 實時監測TDS、溫度、pH等參數,確保系統穩定運行;
? 優先回收利用冷凝水和鹽晶體,降低處理成本與環境負荷。
該工藝適合大型脫硫廢水處理場景(如電廠),通過自動化控制系統(PLC)可實現全流程智能監控,減少人工干預。
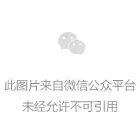
蒸發結晶法處理脫硫廢水的具體操作步驟需結合水質特性與工藝目標,從預處理到最終產物處置形成完整閉環,以下是分階段的詳細流程及技術要點:
一、預處理階段:雜質去除與水質優化
1. 中和調pH與重金屬沉淀
? 操作流程:
? 廢水先進入調節池均質,通過pH在線監測儀控制,投加石灰乳(Ca(OH)?)或NaOH溶液,將pH調節至8.5-9.5。此時Fe3?、Cu2?等重金屬離子生成氫氧化物沉淀(如Fe(OH)?、Cu(OH)?)。
? 投加硫化鈉(Na?S)或有機硫捕集劑(如TMT-15),與Hg2?、Pb2?等頑固重金屬反應生成硫化物沉淀(溶度積低至10?3?以下),強化去除效果。
? 關鍵參數:
? pH控制精度±0.3,反應停留時間≥30分鐘,硫化物投加量為理論值的1.2-1.5倍。
2. 混凝絮凝與固液分離
? 操作流程:
? 投加聚合氯化鋁(PAC)作為混凝劑(50-100 mg/L),通過攪拌(轉速150-200 rpm,10分鐘)形成膠體顆粒;再投加聚丙烯酰胺(PAM,陰離子型,5-10 mg/L),低速攪拌(30-50 rpm,20分鐘)促進絮體長大。
? 混合液進入斜板沉淀池或板框過濾器,通過重力沉降或壓力過濾去除懸浮物(SS≤50 mg/L),濾液進入中間水池。
? 設備要求:
? 沉淀池表面負荷≤1.0 m3/(㎡·h),過濾器濾速≤8 m/h,定期反洗(水反洗+氣反洗)維持過濾效率。
3. 軟化除硬度(鈣鎂離子)
? 操作流程:
? 向中間水池投加碳酸鈉(Na?CO?),與Ca2?反應生成CaCO?沉淀;投加NaOH使Mg2?生成Mg(OH)?沉淀,反應pH控制在10-11,停留時間≥40分鐘。
? 軟化后廢水經砂濾器進一步去除細小顆粒,使鈣鎂離子濃度≤10 mg/L,避免蒸發結垢。
二、蒸發濃縮階段:高效減量化處理
1. 多效蒸發(MEE)工藝操作
? 典型3效流程:
1. 第一效蒸發器:
? 預處理后的廢水經預熱器升溫至60-70℃,進入第一效蒸發器,利用生蒸汽(0.5-0.8 MPa)加熱至80-90℃,產生二次蒸汽(約70℃)和濃縮液(TDS提升至10000-15000 mg/L)。
2. 第二/三效蒸發器:
? 第一效二次蒸汽作為第二效熱源,加熱溫度降至60-70℃,二次蒸汽再進入第三效(溫度50-60℃),最終濃縮液TDS達30000-50000 mg/L,蒸汽利用率提升至300%-500%(相比單效)。
? 控制要點:
? 各效壓力梯度:第一效0.1 MPa(表壓),第二效0.05 MPa,第三效負壓(-0.03 MPa),通過真空泵維持負壓狀態。
2. 機械蒸汽再壓縮(MVR)工藝操作
? 核心流程:
? 廢水進入MVR蒸發器,通過電加熱或低壓蒸汽升溫至沸點(如70℃),蒸發產生的二次蒸汽經羅茨壓縮機壓縮(壓力升至0.15 MPa,溫度升至85℃),返回蒸發器作為熱源,形成閉式循環。
? 能耗優勢:
? 單位水蒸發能耗約20-30 kWh/m3(MEE為80-120 kWh/m3),但需定期維護壓縮機(每5000小時更換潤滑油)。
三、結晶分離階段:鹽晶析出與固液分離
1. 強制循環結晶器操作
? 蒸發結晶(以NaCl為例):
? 濃縮液(TDS 30000-50000 mg/L)進入結晶器,通過循環泵(流量為處理量的5-10倍)強制循環,攪拌轉速60-80 rpm,維持蒸發溫度70-80℃,使NaCl過飽和結晶。
? 當溶液密度達1.2-1.3 g/cm3時,啟動晶漿排出泵,將混合液送入旋流器。
2. 固液分離與晶體處理
? 旋流器+離心機組合:
? 旋流器(直徑100-200 mm)分離出粗晶體(粒徑>50 μm),底流進入臥式螺旋離心機(轉速3000-4000 rpm)脫水,得到含水率<8%的鹽餅;溢流返回結晶器繼續濃縮。
? 晶體洗滌與干燥:
? 鹽餅用冷凝水洗滌(固液比1:1),去除表面附著的重金屬離子,經流化床干燥器(溫度100-120℃)烘干,得到工業鹽(NaCl純度≥95%)。
四、后續處理與系統維護
1. 冷凝水回用處理
? 深度處理流程:
? 蒸發冷凝水(TDS<100 mg/L)進入中和池,投加稀硫酸將pH調至6-9,經活性炭過濾器(濾速10-15 m/h)吸附微量有機物,達標后回用于電廠循環水系統或脫硫工藝補水。
2. 鹽餅處置與危廢判定
? 資源化利用:
? 若鹽餅中重金屬(Hg≤0.001%、As≤0.005%)符合《工業鹽》(GB/T 5462)標準,可出售給氯堿廠或融雪劑企業;若重金屬超標,需經固化處理(如水泥固化,固液比2:1)后送危廢填埋場。
3. 結垢與腐蝕控制
? 在線防垢措施:
? 向蒸發器循環液中投加聚環氧琥珀酸(PESA)阻垢劑(5-10 mg/L),抑制CaSO?、Mg(OH)?結晶;每72小時用2%檸檬酸溶液循環清洗換熱管(溫度60℃,時間2小時),維持傳熱系數≥800 W/(㎡·K)。
? 防腐材料選型:
? 蒸發器主體采用TA2鈦合金(耐氯離子腐蝕),管道內襯聚四氟乙烯(PTFE),泵葉輪選用2205雙相不銹鋼,閥門密封件采用氟橡膠。
五、自動化控制與安全操作
? PLC控制系統:
? 實時監測蒸發溫度、壓力、液位、TDS等參數,自動調節進料量、蒸汽流量及結晶器攪拌速度,異常時(如結垢導致溫差>5℃)觸發報警并啟動清洗程序。
? 安全聯鎖:
? 結晶器設置超壓保護(安全閥開啟壓力0.2 MPa),蒸汽管道安裝壓力傳感器,當壓縮機溫度>90℃時自動停機冷卻。
工藝總結與優化方向
? 關鍵優勢:處理效率高(單日處理量可達100-1000 m3),鹽晶回收率≥90%,冷凝水回用率≥95%;
? 優化點:針對高硫酸鹽廢水(如SO?2?>20000 mg/L),可采用“蒸發+冷卻結晶”組合工藝(先蒸發除NaCl,再冷卻至20℃析Na?SO?·10H?O),提升晶體純度;
? 適用場景:適用于燃煤電廠、鋼鐵廠等連續產生高鹽脫硫廢水的場景,尤其適合TDS>10000 mg/L的廢水處理。在蒸發結晶法處理脫硫廢水時,結垢(如CaCO?、CaSO?、Mg(OH)?等晶體沉積)會顯著影響設備效率,需從預處理、工藝控制、設備維護等多維度綜合防控,具體措施如下:
一、預處理階段:源頭減少結垢離子
1. 深度軟化除硬
? 鈣鎂離子去除:
? 投加過量碳酸鈉(Na?CO?)和氫氧化鈉(NaOH),將Ca2?、Mg2?濃度降至5 mg/L以下(理論溶解度極限),反應pH控制在10.5-11,通過板框壓濾機分離沉淀,避免蒸發階段生成CaCO?或Mg(OH)?垢。
? 硫酸鹽控制:
? 若廢水中SO?2?濃度高(>5000 mg/L),可投加氯化鋇(BaCl?)生成BaSO?沉淀(Ksp=1.1×10?1?),但需嚴格控制Ba2?殘留量(≤0.1 mg/L,避免毒性風險)。
2. 有機物與膠體去除
? 強化混凝:
? 增加聚合氯化鋁(PAC)投加量至100-150 mg/L,配合陽離子型聚丙烯酰胺(PAM),通過混凝-沉淀去除腐殖酸等有機物,防止其與金屬離子形成黏性復合垢。
二、蒸發階段:工藝參數優化與防垢技術
1. 操作條件調控
? 溫度與濃度控制:
? 多效蒸發(MEE)中,將末效溫度控制在50-60℃(避免CaSO?·2H?O在70℃以上快速結晶),濃縮液TDS不超過30000 mg/L(過飽和極限),通過在線TDS儀表實時監控,達到閾值時及時排出晶漿。
? 流速與湍流強度:
? 蒸發器循環液流速≥1.5 m/s(強制循環泵驅動),使流體在換熱管內形成湍流,減少晶體沉積機會;結晶器攪拌轉速提升至80-100 rpm,打碎初始晶核,促進均勻結晶。
2. 化學阻垢劑投加
? 藥劑選型與用量:
? 選用聚羧酸類阻垢劑(如聚環氧琥珀酸PESA、聚丙烯酸PAA),投加量5-10 mg/L,通過螯合Ca2?、Mg2?降低離子活性,同時分散微小晶體防止聚集;針對硫酸鹽垢,可復配膦酸鹽(如ATMP),用量3-5 mg/L。
三、設備設計與材料選型
1. 換熱面抗結垢設計
? 表面處理:
? 蒸發器換熱管采用鈦合金(TA2)或2205雙相不銹鋼,內壁拋光至粗糙度Ra≤0.8 μm,減少晶體附著點;采用螺旋纏繞式換熱管(增加湍流),或設置超聲波振動裝置(頻率20-40 kHz),通過空化效應剝離初期垢層。
2. 結構優化
? 強制循環與晶漿分離:
? 結晶器采用外循環式設計,循環管直徑比內管大30%,降低流體阻力;在換熱管入口設置布液器,避免局部流速過低導致結垢。
四、在線清洗與維護策略
1. 周期性化學清洗
? 酸洗方案:
? 當換熱溫差超過5℃時,用2%檸檬酸溶液(pH 3-4,溫度60℃)循環清洗2小時,溶解碳酸鹽垢;若存在硫酸鹽垢,可改用5%硝酸銨溶液(配合緩蝕劑,如烏洛托品),清洗后用清水沖洗至pH中性。
2. 機械清洗輔助
? 高壓水射流:
? 每年停機檢修時,用高壓水槍(壓力100-150 MPa)沖洗蒸發器內壁及換熱管,去除頑固垢層;對于管程結垢,可采用海綿球在線清洗系統(直徑比管徑大1-2 mm的橡膠球,每天循環30分鐘)。
五、智能監控與預警
1. 結垢預測模型
? 在線監測參數:
? 通過電導率儀、pH計、溫度傳感器實時計算溶液的朗格利爾指數(LSI)和雷茲納指數(RSI),當LSI>0.5時(表明有結垢趨勢),自動加大阻垢劑投加量或啟動清洗程序。
2. 自動化控制
? 聯動調節:
? 當結晶器內濁度突然下降(可能因晶體沉積導致),PLC系統自動增加循環流量10%-20%,同時提升攪拌轉速,防止垢層快速增厚。
六、工藝改進與創新
1. 分鹽結晶工藝
? 分段除垢:
? 對含高硫酸鹽的脫硫廢水,先通過蒸發去除NaCl(控制溫度80℃),再將母液冷卻至20℃使Na?SO?·10H?O結晶,避免硫酸鹽與碳酸鹽在同一階段結垢,同時提升鹽晶純度。
2. 膜法預處理協同
? 納濾(NF)分鹽:
? 在蒸發前采用納濾膜分離Ca2?、Mg2?(截留率>95%),使進入蒸發器的廢水硬度<50 mg/L,從源頭降低結垢風險,同時膜產水可直接回用,減少蒸發負荷。
總結
結垢控制需結合“源頭軟化-過程阻垢-設備抗結-實時清洗”的全流程策略,其中預處理階段的鈣鎂離子去除率需達99%以上,蒸發過程中阻垢劑投加量與溫度控制是關鍵,配合周期性化學清洗(每72小時一次)和抗結垢材料選型,可將設備運行周期延長至30天以上,顯著降低維護成本。近年來,隨著環保標準提升和資源化需求增加,脫硫廢水處理技術向高效、低耗、資源化方向發展,以下是幾類新型技術及應用進展:
一、膜法集成技術
1. 正滲透(FO)- 膜蒸餾(MD)耦合工藝
? 原理:利用FO膜(如醋酸纖維素膜)以高濃度鹽水(如NaCl溶液)為汲取液,分離廢水中的水和鹽分,再通過MD膜(疏水性PVDF膜,孔徑0.1-0.4 μm)進一步凈化產水,鹽截留率>99.5%。
? 優勢:能耗較傳統蒸發降低30%-40%,無結垢風險(操作溫度<60℃),產水可直接回用至鍋爐補給水系統。
2. 高壓納濾(HFNF)分鹽技術
? 創新點:采用耐高壓納濾膜(操作壓力1.5-2.0 MPa),選擇性分離廢水中的Na?/Ca2?/Mg2?,實現NaCl與硫酸鹽的分離,產出純度>95%的工業鹽(如NaCl),同時降低蒸發負荷。
二、電化學技術
1. 電化學氧化-結晶一體化設備
? 核心工藝:
? 通過鈦基二氧化釕(Ti/RuO?)陽極電解廢水,利用·OH自由基氧化有機物(COD去除率>80%),同時電解產生的Ca2?/Mg2?與OH?反應生成沉淀,同步去除硬度;電解后廢水經MVR蒸發結晶,鹽晶純度提升至98%以上。
? 案例:某300 MW電廠應用該技術,噸水能耗降至8-10 kWh,較傳統工藝節約蒸汽消耗50%。
2. 電吸附(EST)脫鹽技術
? 原理:利用多孔電極(如活性炭纖維)在電場作用下吸附水中離子,當電極飽和后通過反沖洗再生,適用于低濃度脫硫廢水(TDS<5000 mg/L)的深度脫鹽,產水TDS<100 mg/L。
三、蒸發結晶工藝創新
1. 機械蒸汽再壓縮(MVR)+ 分鹽結晶
? 升級點:
? 采用離心式壓縮機回收蒸發產生的二次蒸汽(能量利用率提升至90%),結合多級閃蒸分鹽(先蒸出NaCl,再冷卻結晶Na?SO?),鹽晶可達到《工業鹽》(GB/T 5462-2015)精制鹽標準,實現資源化利用。
2. 負壓低溫蒸發(VLE)技術
? 優勢:操作壓力<5 kPa,溫度<40℃,避免CaSO?等鹽類結晶,適合高硫酸鹽廢水處理,設備材質可選316L不銹鋼(成本降低40%),且無結垢風險(運行周期>60天)。
四、資源化利用技術
1. 脫硫廢水制脫硫劑(CaCO?)
? 工藝路線:
? 廢水經預處理去除重金屬后,通入CO?氣體(來自電廠煙道氣),與Ca2?反應生成高純度CaCO?(純度>97%),可回用于脫硫系統,實現“以廢治廢”。某2×600 MW機組應用該技術,年節約脫硫劑成本約800萬元。
2. 蒸發結晶鹽資源化分級利用
? 分質結晶:通過控制蒸發溫度和pH,先結晶出NaCl(用于氯堿工業),再結晶出Na?SO?(用于造紙),母液中的微量重金屬(如Hg、As)通過螯合樹脂吸附去除,最終實現零排放。
五、生物處理技術創新
1. 嗜鹽微生物協同處理系統
? 應用場景:針對低濃度脫硫廢水(TDS<10000 mg/L),采用嗜鹽菌(如Halomonas屬)降解有機物,同時通過微生物代謝產生的碳酸酐酶促進CaCO?結晶,同步去除硬度和COD(去除率分別達90%和70%)。
2. 藻類-膜生物反應器(A-MBR)
? 原理:利用小球藻吸收廢水中的N、P等營養物質,結合MBR膜分離,產水可回用至循環水系統,藻類生物質經干燥后可作為生物燃料,實現“廢水處理+資源回收”雙重目標。
六、高級氧化技術(AOPs)聯用
1. 臭氧-紫外(O?-UV)組合工藝
? 作用:UV光催化O?產生·OH,強化降解廢水中的有機膦酸鹽(如ATMP)和腐殖酸(TOC去除率>90%),為后續膜法或蒸發工藝創造條件,減少結垢和膜污染。
2. 過硫酸鹽(PDS)活化氧化
? 創新:通過Fe2?或非均相催化劑(如Fe?O?@C)活化PDS產生SO?·?自由基,氧化電位達2.5-3.1 V,可快速分解廢水中的難降解有機物,反應時間縮短至30分鐘以內。
技術對比與應用建議
技術類型 適用廢水特征 噸水處理成本 關鍵優勢 典型應用場景
FO-MD耦合 高鹽高硬度 8-12元 低能耗、無結垢 缺水地區電廠
MVR分鹽結晶 高TDS(>50000 mg/L) 15-20元 鹽資源化、零排放 新建環保標桿電廠
電化學氧化 高有機物、重金屬 10-15元 一體化設備、占地小 老電廠改造
脫硫廢水制CaCO? 高Ca2?、低重金屬 5-8元 以廢治廢、成本低 配套石灰石-石膏脫硫系統電廠
總結
新型技術正從“達標排放”向“資源化利用”轉型,膜法與蒸發結晶的耦合、電化學技術的低耗化、以及分鹽結晶的精細化是未來發展方向。實際應用中需結合廢水水質(如硬度、有機物含量)、地域水資源政策(如零排放要求)及經濟性,選擇“預處理+核心工藝+資源回收”的組合方案,例如:高硬度廢水優先采用“HFNF分鹽+MVR結晶”,高有機物廢水可選用“O?-UV氧化+MD膜蒸餾”。
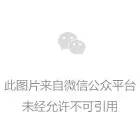
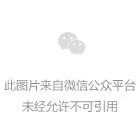
用于脫硫廢水處理的膜法集成技術通過不同膜工藝的組合,實現高效脫鹽、分質處理及資源化利用,以下是幾類典型技術及原理、優勢解析:
一、正滲透(FO)- 膜蒸餾(MD)耦合工藝
1. 核心原理
? FO階段:以高濃度NaCl溶液為汲取液,利用滲透壓差驅動脫硫廢水中的水分子透過FO膜(如醋酸纖維素膜),鹽分和大分子污染物被截留。
? MD階段:FO產水進入疏水性MD膜(如PVDF膜,孔徑0.1-0.4 μm),通過熱側(<60℃)蒸汽壓差異使水分子透過膜孔,進一步凈化產水。
2. 技術優勢
? 低能耗:無需高壓驅動,能耗較傳統蒸發降低30%-40%。
? 抗結垢:操作溫度低,避免Ca2?、Mg2?等在膜表面結晶,運行周期可達90天以上。
? 產水水質優:鹽截留率>99.5%,產水可直接回用至鍋爐補給水系統。
二、高壓納濾(HFNF)分鹽技術
1. 工藝特點
? 采用耐高壓納濾膜(操作壓力1.5-2.0 MPa),利用膜孔篩分效應和電荷排斥作用,選擇性分離廢水中的Na?、Ca2?、Mg2?等離子。
? 分鹽邏輯:優先截留Ca2?、Mg2?及硫酸鹽,使透過液以NaCl為主,實現硫酸鹽與氯化鈉的初步分離。
2. 應用價值
? 降低蒸發負荷:分鹽后蒸發水量減少30%-50%,結晶鹽純度提升至95%以上(滿足工業鹽標準)。
? 資源化導向:透過液經進一步處理可產出精制NaCl,截留液可回收硫酸鹽或作為固廢處理。
三、膜集成預處理-蒸發耦合工藝
1. 典型組合:UF+RO+MVR
? 預處理:超濾(UF)去除懸浮物和膠體,反滲透(RO)脫鹽(脫鹽率>98%),RO濃水進入機械蒸汽再壓縮(MVR)蒸發結晶。
? 優勢:RO產水回用,濃水減量后蒸發,總能耗較傳統全蒸發降低25%-30%,適合TDS<10000 mg/L的廢水。
2. 工藝優化:NF分鹽+RO濃縮
? 通過納濾(NF)先分離廢水中的一價鹽(如NaCl)和多價鹽(如CaSO?),一價鹽透過液經RO濃縮后蒸發,多價鹽截留液單獨處理,減少蒸發結晶中的結垢風險。
四、膜接觸器(MC)脫氨技術
1. 原理
? 利用疏水性中空纖維膜(如PP膜)作為氣液界面,廢水側調節pH至11以上,NH?以分子態透過膜孔,被另一側的稀硫酸吸收生成硫酸銨,實現氨氮(>1000 mg/L)的高效去除(脫除率>99%)。
2. 與膜法集成應用
? 與RO或NF聯用,先脫除氨氮避免蒸發過程中NH?揮發污染,同時回收硫酸銨作為化肥原料,實現“廢水處理+資源回收”。
五、膜法與電化學聯用技術
1. 電滲析(ED)- 電化學氧化耦合
? ED階段:通過離子交換膜分離廢水中的鹽分,濃水側進入電化學氧化槽(Ti/RuO?陽極),利用·OH自由基氧化有機物并沉淀重金屬。
? 優勢:分鹽效率高(NaCl回收率>90%),同時降解COD(去除率>80%),為后續結晶提供清潔水質。
技術對比與適用場景
技術類型 適用廢水特征 核心優勢 典型問題及應對
FO-MD耦合 高鹽高硬度(TDS>30000 mg/L) 低能耗、抗結垢 汲取液需回收(如NaCl循環)
HFNF分鹽 含硫酸鹽、需分質結晶 精準分鹽、降低蒸發負荷 膜污染需定期化學清洗(CIP)
UF+RO+MVR 中等鹽濃度(TDS<10000 mg/L) 產水回用率高(>70%) RO濃水仍需蒸發處理
膜接觸器脫氨 高氨氮(>500 mg/L) 氨氮回收、無二次污染 需調節pH至堿性(成本增加)
總結
膜法集成技術通過“分離-濃縮-分鹽”的協同作用,在脫硫廢水處理中展現出低耗、高效、資源化的優勢。實際應用中,需根據廢水水質(如硬度、氨氮、有機物含量)選擇適配的膜組合,例如高硬度廢水優先采用HFNF分鹽,高氨氮廢水可結合膜接觸器脫氨,而缺水地區更適合FO-MD耦合工藝以實現產水回用。未來,膜材料的耐污染性(如親水性改性)和工藝的智能化控制(如在線膜污染監測)將是技術優化的重點方向。以下是幾種典型膜法集成技術在脫硫廢水處理中的優缺點分析,結合工藝原理與實際應用場景展開:
一、正滲透(FO)-膜蒸餾(MD)耦合工藝
優點
? 低能耗特性:依賴滲透壓差和蒸汽壓差驅動,無需高壓泵(能耗較RO降低30%-40%),適合能源成本高的場景。
? 抗結垢能力強:MD操作溫度<60℃,減少Ca2?、Mg2?等無機鹽結晶,膜通量衰減緩慢(運行周期可達3個月以上)。
? 產水水質優:鹽截留率>99.5%,產水可直接回用于鍋爐補給水,實現“零排放”目標。
缺點
? 汲取液回收成本高:需定期回收FO階段的高濃度NaCl汲取液,增加蒸發或結晶設備投入(占總投資的20%-30%)。
? 膜污染難控制:廢水中有機物易吸附在FO膜表面,需頻繁化學清洗(CIP),影響連續運行穩定性。
二、高壓納濾(HFNF)分鹽技術
優點
? 精準分鹽效率高:通過電荷排斥與篩分效應分離一價鹽(NaCl)和多價鹽(CaSO?),分鹽純度>90%,為結晶鹽資源化奠定基礎。
? 降低蒸發負荷:分鹽后蒸發水量減少30%-50%,結晶鹽中NaCl純度提升至95%以上,符合工業鹽標準。
缺點
? 操作壓力高(1.5-2.0 MPa):膜組件耐壓要求高,設備投資比普通納濾增加15%-20%,且膜壽命較短(通常1-2年)。
? 濃水需后續處理:截留的多價鹽濃水(如CaSO?)仍需化學沉淀或蒸發處理,存在固廢處置成本。
三、UF+RO+MVR膜集成預處理-蒸發工藝
優點
? 產水回用率高:RO產水回用率>70%,適用于缺水地區,減少新水用量;MVR蒸發能耗較傳統多效蒸發降低30%。
? 工藝成熟度高:UF預處理去除懸浮物,RO脫鹽,MVR結晶,各環節技術成熟,運維難度低。
缺點
? RO濃水仍需蒸發:RO濃水TDS可達50000 mg/L以上,蒸發量仍較大,且高硬度濃水易導致MVR換熱器結垢。
? 對有機物敏感:廢水中COD>500 mg/L時,RO膜易受有機物污染,需增加預處理(如臭氧氧化),提升成本。
四、膜接觸器(MC)脫氨技術
優點
? 氨氮回收效率高:調節pH至11后,氨氮脫除率>99%,生成的硫酸銨可作為化肥原料,實現資源回收(噸水收益約5-10元)。
? 無二次污染:氨氮以硫酸銨形式回收,避免傳統吹脫法的NH?揮發污染,符合環保要求。
缺點
? 堿液投加成本高:需投加NaOH調節pH至強堿性,噸水藥劑成本增加8-15元,且易導致膜孔堵塞(Ca(OH)?沉淀)。
? 僅針對氨氮處理:無法去除廢水中的鹽分和重金屬,需與其他膜工藝(如RO)聯用才能實現全流程處理。
五、電滲析(ED)-電化學氧化聯用技術
優點
? 分鹽與凈化協同:ED分鹽效率>90%,電化學氧化同步降解COD(去除率>80%)并沉淀重金屬(如Cu2?、Pb2?)。
? 能源回收潛力:電化學過程可利用太陽能等可再生能源,降低能耗成本(較傳統工藝降低15%-20%)。
缺點
? 電極損耗快:Ti/RuO?陽極長期使用后催化活性下降,更換周期約6-12個月,電極成本占總投資的15%-20%。
? 高鹽廢水適應性差:TDS>20000 mg/L時,ED膜電阻增大,能耗急劇上升,需先經RO濃縮預處理。
技術對比與應用建議
技術類型 核心優勢 主要缺點 適用場景
FO-MD耦合 低能耗、抗結垢 汲取液回收成本高 高鹽高硬度廢水,需產水回用場景
HFNF分鹽 精準分鹽、結晶鹽資源化 高壓操作成本高 含硫酸鹽廢水,需分質結晶場景
UF+RO+MVR 工藝成熟、產水回用率高 RO濃水蒸發負荷大 中等鹽濃度廢水,現有電廠改造項目
膜接觸器脫氨 氨氮回收、無廢氣污染 堿液投加成本高 高氨氮廢水(>500 mg/L)的預處理
ED-電化學聯用 分鹽與凈化一體化 電極損耗快 高COD、含重金屬的復雜廢水處理
總結
膜法集成技術在脫硫廢水處理中展現出“高效分離+資源回收”的優勢,但需權衡能耗、投資與運維成本。例如,FO-MD適合追求低能耗的新建項目,而UF+RO+MVR更適合現有電廠的改造升級。實際應用中,常采用“膜法分鹽+蒸發結晶”的組合工藝,通過膜技術減少蒸發負荷,同時結合水質特性優化預處理(如加藥軟化去除鈣鎂離子),以降低膜污染和結垢風險,最終實現“減量化、無害化、資源化”目標。未來,開發耐污染復合膜材料(如聚酰亞胺改性膜)和智能化膜污染預警系統,將是提升技術經濟性的關鍵方向。用于脫硫廢水處理的膜法集成技術投資成本因具體工藝、處理規模、設備選型等因素有所不同,以下是一些常見膜法集成技術投資成本的大致情況:
? 正滲透(FO)-膜蒸餾(MD)耦合工藝:設備投資較高,預處理設備、FO和MD膜組件及相關配套設備等,處理規模為100立方米/天的項目,投資可能在500 - 800萬元左右。
? 高壓納濾(HFNF)分鹽技術:包括預處理系統、納濾膜裝置等,對于處理規模為50 - 100立方米/天的脫硫廢水,投資成本大概在300 - 600萬元。
? UF + RO + MVR膜集成預處理 - 蒸發工藝:工藝較為成熟,投資成本相對穩定,以處理規模為200立方米/天的系統為例,設備、土建、安裝等總投資可能在1000 - 1500萬元。
? 膜接觸器(MC)脫氨技術:主要涉及膜接觸器設備、pH調節裝置等,若處理規模為80 - 120立方米/天,投資成本可能在300 - 500萬元。不過通常需與其他膜工藝聯用,會增加整體投資。
? 電滲析(ED)-電化學氧化聯用技術:包含電滲析設備、電化學氧化裝置等,處理規模為100立方米/天左右的項目,投資可能在400 - 700萬元。
以上數據僅為估算,實際投資成本需根據具體項目的詳細設計和市場行情進行準確核算。以下是一些膜法集成技術在脫硫廢水處理中的應用案例:
某燃煤電廠脫硫廢水零排放項目
? 項目概況:某燃煤電廠建設規模為2×350MW超臨界間接空冷供熱機組,實施了脫硫廢水零排放工程項目。
? 工藝路線:預處理系統采用兩級軟化澄清+多介質過濾器+弱酸陽床;濃縮系統采用納濾+兩級反滲透;結晶系統采用MVR強制循環閃蒸工藝。
? 運行情況:該工藝于2018年8月底投入生產運行,2020年初主體設備均退出運行。運行中存在預處理單元堵塞、膜系統污堵、噴霧干燥器無法正常干燥結晶、MVR強制循環蒸發結晶無法建立熱平衡等問題。原因是對脫硫廢水水質變化預估不充分,實際硫酸根離子和懸浮物濃度遠超設計值。
DTRO膜法處理脫硫廢水項目
? 技術特點:采用DTRO膜法,具有施工周期短、運行成本低、靈活性強、適應性強等特點。
? 處理效果:可解決脫硫廢水中高鹽量、高濁度、高硬度的問題,出水可直接回用,實現水資源的優化利用,能使脫硫廢水實現近零排放。膜法集成技術在脫硫廢水零排放項目成本中占比較高,通常能達到總投資的30% - 60%左右。
在“預處理 + 濃縮減量 + 末端固化”的脫硫廢水零排放處理系統中,膜法集成技術主要應用于濃縮減量環節,是現階段的主流濃縮技術。如采用“預處理軟化 + 納濾分鹽 + 膜濃縮 + 蒸發結晶”工藝的項目,膜法集成技術中的納濾、膜濃縮等設備及相關配套設施投資,在總投資中占比較大。
不過,具體占比會因項目的處理規模、工藝復雜程度、膜組件的選型和品牌等因素有所不同。處理規模大、對水質要求高、采用先進高效膜組件的項目,膜法集成技術投資占比可能會更高。膜法集成技術在脫硫廢水零排放項目中的具體應用如下:
1. 管式超濾膜軟化:向脫硫廢水中投加石灰、氫氧化鈉和碳酸鈉,經反應后由管式超濾膜過濾,基本去除廢水中的硬度,防止后續反滲透膜結垢。
2. 納濾膜分鹽:預處理軟化后的廢水經納濾膜處理,將廢水中的一價離子和二價離子分離,產水中成分主要為氯化鈉,為蒸發結晶高純度工業鹽奠定基礎。
3. 高壓反滲透膜濃縮:采用高壓反滲透膜對納濾膜產水進行濃縮減量,淡水回用,濃水進入蒸發結晶系統,可大大降低廢水蒸發量,節約能耗。
4. 碟管式反滲透(DTRO)進一步濃縮:部分項目中,高鹽反滲透的濃水送往DTRO進行進一步濃縮,該技術適應性強,可根據進水含鹽量指標,采用不同壓力級別的DTRO膜處理,且膜系統污染較小。
5. MVR蒸發結晶:采用機械蒸汽壓縮再循環蒸發結晶技術將膜濃縮后的廢水進行蒸發結晶,生產工業鹽,實現廢水零排放和資源回收利用。

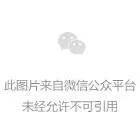
膜法集成技術在脫硫廢水處理中具有以下優勢:
高效分離與凈化
? 能精準去除廢水中的懸浮物、鹽分、重金屬等污染物,分離效率高,出水水質穩定,可滿足回用或排放標準。例如納濾膜能有效分離一價和二價離子,為分鹽結晶奠定基礎。
濃縮減量效果顯著
? 通過高壓反滲透、DTRO等膜工藝,可將廢水大幅濃縮,減少后續蒸發結晶的處理量,降低能耗。如高壓反滲透可將廢水濃縮至原體積的10%以下,顯著節約蒸發成本。
資源化利用潛力大
? 結合納濾分鹽、蒸發結晶等工藝,可從廢水中回收氯化鈉、硫酸鈉等工業鹽,實現“零排放”的同時創造經濟效益。例如納濾產水經濃縮結晶后可得到純度較高的工業鹽。
工藝集成度高且靈活
? 可根據廢水水質特點靈活組合超濾、納濾、反滲透等膜工藝,與預處理、蒸發結晶等系統集成,形成閉環處理流程。如“預處理軟化+納濾+RO+MVR”工藝,適應不同項目需求。
自動化程度高,管理便捷
? 膜系統操作相對標準化,可通過自動化控制實現連續運行,減少人工干預,降低運維難度。
占地面積較小
? 相較于傳統蒸發工藝,膜法集成技術的設備緊湊,占地面積約為傳統工藝的1/3~1/2,適合場地受限的電廠項目。膜法集成技術在脫硫廢水處理中存在以下劣勢:
投資成本高
? 膜組件(如納濾膜、高壓反滲透膜)及配套設備(壓力容器、高壓泵等)成本昂貴,加上預處理系統(軟化、過濾等)的投入,整體項目投資比傳統工藝高30%~50%。例如處理規模100m3/天的項目,膜法集成技術投資可能達500萬元以上,而傳統蒸發工藝約300萬元。
膜污染與維護壓力大
? 脫硫廢水含高濃度懸浮物、鈣鎂離子、有機物等,易導致膜表面結垢、膠體污染或生物污染,需頻繁化學清洗(如酸洗、堿洗),甚至更換膜元件。
? 清洗過程中化學藥劑消耗增加運行成本,且膜元件壽命通常為3~5年,更換費用占運維成本的20%~30%。
對水質適應性有限
? 若廢水中懸浮物(SS)超過50mg/L、油類物質超過10mg/L,或pH超出膜耐受范圍(通常pH 2~12),需強化預處理,否則會加速膜污染。
? 當廢水中有機物(如COD)濃度高于100mg/L時,易引發微生物繁殖,影響膜系統穩定性。
能耗與運行成本較高
? 高壓膜工藝(如高壓反滲透、DTRO)需維持10~15MPa的操作壓力,水泵能耗占系統總能耗的40%~50%,噸水處理電耗約8~15kWh,高于傳統混凝沉淀工藝(約2~5kWh/噸)。
? 若廢水硬度高,預處理需投加大量石灰、碳酸鈉,藥劑成本增加約0.5~1元/噸水。
濃縮極限制約零排放
? 膜法濃縮后濃水含鹽量通常達8%~15%,仍需與蒸發結晶聯用才能實現零排放,無法完全替代蒸發工藝。例如高壓反滲透濃水需進一步通過MVR蒸發處理,增加了系統復雜度。
技術復雜性與運維要求高
? 膜系統操作需嚴格控制流量、壓力、溫度等參數,對運維人員專業要求高。若操作不當(如膜組件壓差過高),可能導致膜破損,影響出水水質。
? 部分工藝(如電滲析、膜蒸餾)對設備材質要求高(需耐強酸強堿),維護難度大。膜法集成技術在脫硫廢水處理中面臨的膜污染問題,可通過優化預處理、改進膜工藝及強化運維管理等措施解決,具體如下:
一、優化預處理工藝,從源頭減少污染物
? 強化軟化除硬:投加石灰、碳酸鈉等藥劑,將廢水中鈣鎂離子(硬度)去除至50mg/L以下,避免膜表面結垢。例如采用兩級軟化澄清工藝,第一級投加石灰降低碳酸鹽硬度,第二級投加碳酸鈉去除非碳酸鹽硬度。
? 高效去除懸浮物(SS):通過多介質過濾器、管式超濾(UF)等工藝,將SS控制在10mg/L以下。管式超濾膜孔徑小(0.01~0.1μm),可攔截膠體和細微顆粒,減少膜表面沉積。
? 去除有機物與油類:若廢水中COD較高(>100mg/L),可投加活性炭吸附或臭氧氧化,破壞有機物結構;含油廢水需先經氣浮工藝除油,將油類濃度降至5mg/L以下。
二、改進膜工藝設計,提升抗污染能力
? 選擇抗污染膜組件:采用耐污染型反滲透膜(如聚酰胺復合膜)或碟管式反滲透(DTRO),DTRO的流道寬(6mm)、湍流程度高,可減少懸浮物沉積,適合高濁度廢水。
? 優化膜系統運行參數:
? 降低膜面流速(控制在1~2m/s),減少濃差極化;
? 控制操作壓力在膜耐受范圍內(如高壓RO壓力≤12MPa),避免膜損傷;
? 調節廢水pH至中性(6~8),減少酸/堿對膜的腐蝕。
? 納濾分鹽與濃水回流:通過納濾膜分離一價/二價離子,濃水(含二價鹽)回流至預處理,降低后續RO濃水的結垢風險。
三、強化膜污染控制與清洗維護
? 定期物理清洗:采用清水或低壓沖洗(5~10min/次),去除膜表面松散污染物,每天運行前/后各一次。
? 化學清洗(CIP):根據污染類型選擇藥劑:
? 無機結垢(鈣鎂鹽):用2%檸檬酸+0.1%鹽酸溶液酸洗,溶解碳酸鹽;
? 有機物/膠體污染:用0.1%氫氧化鈉+1%次氯酸鈉溶液堿洗,氧化分解有機物;
? 清洗頻率根據壓差變化調整(當跨膜壓差ΔP上升15%時啟動化學清洗)。
? 膜元件離線清洗與更換:若在線清洗效果不佳,將膜元件拆卸后用專用設備離線清洗,恢復通量;當膜污染嚴重(如脫鹽率下降10%以上),需及時更換膜元件(壽命通常3~5年)。
四、智能化監控與運維管理
? 安裝在線監測儀表(如濁度儀、電導率儀、壓差傳感器),實時監控膜系統運行狀態,提前預警污染風險(如壓差上升、產水量下降)。
? 采用自動加藥系統,根據水質變化精準投加阻垢劑(如聚磷酸鹽),降低結垢概率(投加量約5~10mg/L)。
五、工藝集成與濃水減量
? 將膜法與蒸發工藝結合,如膜濃縮后的濃水(含鹽量8%~15%)進入MVR蒸發結晶,減少膜系統長期運行的濃水積累,避免污染物濃度過高導致膜污染。
? 部分項目采用“膜濃縮+低溫蒸發”組合工藝,降低蒸發能耗的同時,減少膜系統的處理負荷。
案例參考
某電廠脫硫廢水處理項目采用“UF+納濾+高壓RO”工藝,通過強化預處理(兩級軟化+UF)將SS控制在5mg/L以下,同時每周進行1次化學酸洗(檸檬酸溶液)和堿洗(次氯酸鈉溶液),膜系統連續運行3年未出現嚴重污染,通量衰減率<10%。膜法集成技術在脫硫廢水處理中面臨的膜污染問題,主要分為以下幾類,其成因和影響如下:
一、無機結垢污染
? 成因:廢水中高濃度鈣鎂離子(Ca2?、Mg2?)、硫酸根(SO?2?)、碳酸根(CO?2?)等,在膜表面濃縮后形成碳酸鈣(CaCO?)、硫酸鈣(CaSO?)等沉淀。
? 影響:膜表面形成堅硬垢層,導致產水量下降、跨膜壓差(ΔP)升高,脫鹽率降低,甚至堵塞膜孔道。
二、膠體與懸浮物污染
? 成因:廢水中的細微顆粒(如黏土、金屬氧化物)、膠體硅(SiO?)等,在膜表面沉積形成濾餅層。
? 影響:增加膜過濾阻力,產水量快速下降,需頻繁清洗,長期積累會導致膜組件不可逆污染。
三、有機物污染
? 成因:廢水中的腐殖酸、蛋白質、油脂等有機物,通過吸附或沉積附著在膜表面,形成黏性污染物。
? 影響:降低膜通量,改變膜表面電荷性質,加劇其他污染物的吸附,化學清洗難度較大。
四、生物污染(微生物污染)
? 成因:若廢水中含有機物(COD>50mg/L)且預處理不充分,微生物在膜表面繁殖形成生物膜(菌膠團)。
? 影響:生物膜代謝產物堵塞膜孔,產生異味,同時微生物分泌的酶類可能降解膜材料,縮短膜壽命。
五、金屬氧化物污染
? 成因:廢水中的鐵(Fe3?)、錳(Mn2?)等金屬離子,在堿性條件下形成氫氧化物沉淀(如Fe(OH)?),沉積在膜表面。
? 影響:形成深色污染層,降低膜的透水率,且金屬離子可能催化膜材料氧化,加速膜老化。
六、油類污染
? 成因:若廢水中含乳化油或游離油(如設備泄漏油污),油滴附著在膜表面形成疏水性屏障。
? 影響:阻礙水分子通過,產水量大幅下降,且油類與其他污染物結合形成復合污染,清洗難度極高。
污染特征對比與判斷
污染類型 外觀特征 典型成因 清洗藥劑
無機結垢 白色/灰白色堅硬沉積層 鈣鎂離子濃縮結晶 檸檬酸、鹽酸(酸洗)
膠體/懸浮物 黃褐色/灰色濾餅層 細微顆粒與膠體沉積 氫氧化鈉+次氯酸鈉(堿洗)
有機物 棕褐色黏性物質 腐殖酸、油脂吸附 表面活性劑+氧化劑
生物污染 滑膩的膠狀物質,有異味 微生物繁殖 次氯酸鈉(氧化性清洗)
金屬氧化物 紅棕色/黑色沉積層 鐵錳離子氧化沉淀 檸檬酸+還原劑
污染對系統的影響
? 性能下降:產水量減少(可下降30%以上)、脫鹽率降低(如RO膜脫鹽率從99%降至95%以下)。
? 能耗增加:為維持產水量,需提高操作壓力,電耗上升10%~20%。
? 運維成本上升:化學清洗頻率增加(如從每月1次增至每周1次),膜元件更換周期縮短(如從5年提前至2~3年)。
通過水質分析(如檢測鈣鎂離子、COD、油類含量)和膜表面污染特征,可快速判斷污染類型并采取針對性清洗措施。膜法集成技術的膜污染清洗方法需根據污染類型選擇,主要分為物理清洗、化學清洗及特殊清洗技術,具體如下:
一、物理清洗方法
? 清水沖洗:
? 用過濾后的清水(SS<1mg/L)以低壓(0.1~0.2MPa)反向或正向沖洗膜表面,去除松散沉積的懸浮物和膠體。
? 頻率:每天運行前后各1次,每次5~10分鐘,可使膜通量恢復50%~70%。
? 氣水混合沖洗:
? 向沖洗水中通入壓縮空氣(氣壓0.3~0.5MPa),形成氣水湍流,沖擊膜表面污染物(如膠體、有機物)。
? 適用場景:管式超濾(UF)或微濾(MF)膜污染初期,可減少化學藥劑使用。
? 海綿球擦洗:
? 向膜殼內注入彈性海綿球,通過水流推動球體摩擦膜表面,去除硬垢或黏性污染物(如碳酸鈣、油類)。
? 局限:僅適用于直徑>100mm的膜組件(如DTRO),需定期更換海綿球。
二、化學清洗方法(按污染類型分類)
1. 無機結垢污染(鈣鎂鹽、硫酸鹽)
? 酸洗配方:
? 2%檸檬酸溶液(pH=3~4)或0.1%鹽酸溶液,常溫循環清洗30~60分鐘。
? 原理:酸與金屬鹽反應生成可溶性離子,溶解垢層(如CaCO?+2HCl→CaCl?+H?O+CO?↑)。
? 注意事項:鹽酸對金屬材質有腐蝕性,需控制溫度<40℃,清洗后用清水徹底沖洗至中性。
2. 有機物與膠體污染
? 堿洗配方:
? 0.1%氫氧化鈉(NaOH)+1%次氯酸鈉(NaClO)溶液(pH=11~12),循環清洗45~90分鐘。
? 原理:堿液破壞有機物分子結構,次氯酸鈉氧化分解膠體和微生物,降低污染物黏性。
? 案例:某RO膜被腐殖酸污染后,用該配方清洗可使通量恢復90%以上。
3. 生物污染(微生物膜)
? 氧化性清洗:
? 2000~5000ppm次氯酸鈉溶液(pH=8~9),浸泡2~4小時后循環清洗30分鐘。
? 強化方案:若生物膜頑固,可聯合使用過氧化氫(H?O?)+酶制劑(如蛋白酶),分解生物膜基質。
4. 金屬氧化物污染(鐵、錳氫氧化物)
? 還原清洗:
? 1%亞硫酸氫鈉(NaHSO?)+2%檸檬酸溶液,循環清洗60分鐘(溫度控制在25~35℃)。
? 原理:亞硫酸氫鈉將Fe3?還原為Fe2?,檸檬酸絡合金屬離子使其溶解,避免二次沉積。
5. 油類污染
? 表面活性劑清洗:
? 0.5%非離子型表面活性劑(如Triton X-100)+0.1%NaOH溶液,40℃下循環清洗60~90分鐘。
? 輔助措施:清洗前可先用柴油或煤油浸泡膜元件1~2小時,溶解油類(僅適用于耐有機溶劑的膜)。
三、組合清洗工藝
? 先酸后堿交替清洗:
? 適用于復合污染(如無機結垢+有機物),先酸洗去除垢層,再堿洗分解有機物,中間用清水沖洗30分鐘。
? 脈沖式化學清洗:
? 交替進行化學藥劑循環與靜置浸泡(如循環15分鐘+浸泡15分鐘),增強藥劑滲透效果,減少藥劑用量30%以上。
四、離線深度清洗
? 適用場景:在線清洗無效時(通量恢復率<50%),將膜元件拆卸后放入專用清洗槽。
? 工藝步驟:
1. 用高壓水(0.8~1MPa)沖洗膜表面松散污染物;
2. 根據污染類型選擇強酸/強堿或專用清洗劑(如膜廠商提供的復合酶制劑),加熱至35~45℃循環清洗2~4小時;
3. 用去離子水沖洗至出水電導率<10μS/cm,測試膜通量,若恢復率<80%需考慮更換膜元件。
五、預防性清洗與維護
? 定期化學加強反洗(CEB):
? 在膜系統運行中,每隔1~2小時用低濃度藥劑(如50ppm次氯酸鈉)反洗1~2分鐘,抑制微生物繁殖和污染物沉積。
? 阻垢劑投加:
? 在進水端投加有機膦酸鹽類阻垢劑(如ATMP),劑量5~10mg/L,阻止鈣鎂離子結晶,減少結垢風險。
清洗效果判斷與注意事項
? 效果指標:清洗后產水量恢復至初始值的90%以上,跨膜壓差(ΔP)下降15%~20%。
? 禁忌:
? 嚴禁使用硫酸、硝酸等強氧化性酸,避免膜材料氧化;
? 生物污染清洗時,若膜為聚酰胺材質,次氯酸鈉濃度需<1000ppm,防止膜水解。
通過污染類型快速識別與針對性清洗,可有效延長膜元件壽命(如從3年延長至5年),降低運維成本約20%~30%。在膜法集成技術中,物理清洗和化學清洗的適用性需根據污染類型、膜組件特性及系統運行需求綜合判斷,兩者并無絕對的“更適合”,而是常結合使用。以下從不同維度對比分析:
一、污染類型決定優先選擇
? 物理清洗更適合:
? 輕度污染:如初期懸浮物、膠體沉積(通量下降<10%),物理清洗(清水沖洗、氣水混合)可快速恢復通量,且不損傷膜結構。
? 無機顆粒污染:如泥沙、金屬氧化物顆粒,物理擦洗(海綿球)或高壓水沖洗能直接剝離污染物,避免化學藥劑殘留。
? 化學清洗更適合:
? 頑固污染:如生物膜、有機物凝膠、無機結垢(通量下降>30%),需化學藥劑破壞污染物結構(如酸溶解鈣垢、堿分解有機物)。
? 復合污染:當多種污染物共存時(如有機物+硫酸鹽結垢),化學清洗可通過配方調整實現針對性去除。
二、膜材料與組件類型的影響
? 物理清洗優勢場景:
? 耐沖擊膜組件:如管式膜、平板膜,可承受氣水混合沖洗的湍流沖擊,減少膜絲斷裂風險。
? 敏感膜材料:聚酰胺(PA)材質的反滲透(RO)膜對化學藥劑敏感,物理清洗可降低膜水解或氧化風險。
? 化學清洗優勢場景:
? 抗化學腐蝕膜:如聚偏氟乙烯(PVDF)超濾膜,可耐受次氯酸鈉、酸堿溶液清洗,化學清洗效率更高。
? 中空纖維膜:因膜絲直徑小(0.1~1mm),物理擦洗易導致堵塞,化學循環清洗更易滲透污染層。
三、系統運行成本與效率對比
? 物理清洗:
? 優點:操作簡單、藥劑成本低(僅消耗水和少量壓縮空氣),清洗時間短(5~30分鐘),適合日常維護。
? 缺點:對深層污染(如生物膜基質)效果有限,長期依賴可能導致污染累積。
? 化學清洗:
? 優點:去污徹底,通量恢復率高(可達90%以上),適用于周期性深度清潔。
? 缺點:藥劑成本高(單次清洗約50~200元/支膜),清洗后需大量清水沖洗,且可能縮短膜壽命(如頻繁酸洗加速RO膜脫鹽層降解)。
四、實際應用中的組合策略
? 預處理階段:優先物理清洗(如多介質過濾+超濾預處理),減少進入膜系統的大顆粒污染物,降低化學清洗頻率。
? 日常維護:采用“物理清洗+化學加強反洗(CEB)”組合,例如每天用清水沖洗3次,每周用低濃度次氯酸鈉(50~100ppm)進行CEB,抑制微生物污染。
? 深度修復:當膜污染嚴重時(如跨膜壓差ΔP上升50%),先物理沖洗去除松散污染物,再根據污染類型選擇化學清洗(如酸+堿交替清洗),最大化通量恢復率。
總結:根據場景動態選擇
? 優先物理清洗:適用于污染初期、膜材料敏感、低成本運維需求(如市政水處理)。
? 優先化學清洗:適用于工業廢水處理(高有機物/結垢風險)、污染嚴重且需快速恢復系統性能的場景。
? 最佳實踐:物理與化學清洗結合,形成“預防-維護-修復”的全周期管理,例如:
1. 每天運行前后物理沖洗;
2. 每周進行1次化學CEB;
3. 每3~6個月根據污染監測數據(如SDI值、TOC去除率)進行針對性化學清洗。
這種策略可在保證膜壽命的同時,將清洗成本降低30%以上,是膜法集成技術的主流運維模式。在膜法集成技術中,物理清洗和化學清洗的操作步驟因污染類型、膜組件形式不同而略有差異,但核心流程具有通用性。以下是兩類清洗方法的標準操作步驟及注意事項:
一、物理清洗操作步驟
1. 清水沖洗(最常用)
? 步驟1:停機與排水
停止膜系統運行,打開產水側和濃水側閥門,排出膜殼內殘留液體(防止污染物沉積)。
? 步驟2:正向沖洗
用原水或產水以1.5~2倍正常運行流量從進水側沖洗,持續10~15分鐘,水流方向與運行時一致,沖掉膜表面松散顆粒(如泥沙、膠體)。
? 步驟3:反向沖洗(可選)
若為中空纖維膜或平板膜,可從產水側反向進水沖洗(流量為正向的50%),剝離膜絲內側污染物,持續5~10分鐘(注意:反滲透膜嚴禁反向沖洗,避免膜卷變形)。
? 步驟4:氣水混合沖洗(強化版)
向沖洗水中通入壓縮空氣(氣壓0.2~0.3MPa),形成氣水脈沖流,對管式膜或超濾膜進行3~5次脈沖沖洗(每次30秒),利用氣泡爆破力震落頑固顆粒。
2. 機械擦洗(針對特定組件)
? 海綿球擦洗(適用于管式膜)
將直徑略大于管徑的海綿球從進水側推入,通過水流推動海綿球摩擦膜內壁,每根膜管重復3~5次,清除無機垢或生物膜。
二、化學清洗操作步驟
1. 清洗前準備(關鍵前提)
? 污染類型判斷:通過SDI(污染指數)、膜面采樣鏡檢(如發現菌絲則為生物污染)、系統壓差變化(ΔP上升>15%)確定藥劑類型:
? 有機物污染:用堿液(NaOH+表面活性劑);
? 無機結垢:用酸液(檸檬酸/鹽酸);
? 生物污染:用氧化劑(次氯酸鈉/過硫酸鉀)。
? 藥劑配制:按膜廠商推薦濃度(如RO膜酸洗:2%檸檬酸,pH=3;堿洗:1% NaOH+0.02% SDS),用去離子水溶解,控制溫度25~35℃(提升溶解效率)。
2. 標準化學清洗流程
? 步驟1:循環清洗
用清洗泵將藥劑從進水側打入膜系統,以50~80%設計流量循環(避免高壓導致膜損傷),持續30~60分鐘,同時監測清洗液顏色(如變渾濁需更換藥劑)。
? 步驟2:浸泡清洗
循環結束后關閉泵,讓藥劑在膜殼內浸泡1~2小時(生物污染需延長至4小時),通過化學作用分解污染物基質(如次氯酸鈉破壞生物膜EPS層)。
? 步驟3:脈沖清洗(強化版)
浸泡后開啟清洗泵,以30秒開/30秒停的脈沖模式循環15分鐘,利用水流沖擊增強藥劑滲透。
? 步驟4:清水沖洗
用產水或反滲透水沖洗膜系統,直至出水pH與進水一致(避免藥劑殘留),沖洗時間需>30分鐘(化學清洗后必須徹底沖洗,否則藥劑殘留會加速膜老化)。
3. 復合污染的交替清洗
? 若同時存在有機物+無機垢,按“堿洗→酸洗→氧化劑清洗”順序分步進行,每步間隔清水沖洗至中性,防止藥劑反應沉淀(如堿洗后直接酸洗可能生成金屬氫氧化物沉淀)。
三、操作注意事項
物理清洗
? 沖洗水溫需控制在15~35℃(低溫導致水黏度上升,沖洗效率下降);
? 中空纖維膜反洗壓力≤0.1MPa,避免膜絲破裂(尤其是PVDF材質)。
化學清洗
? 藥劑pH控制:RO膜酸洗pH≥2(防止膜脫鹽層水解),堿洗pH≤11;
? 次氯酸鈉濃度≤200ppm(聚酰胺膜耐氯性差,超過此濃度需添加硫代硫酸鈉中和余氯);
? 清洗后若系統暫不運行,需用1%亞硫酸鈉溶液保護膜,防止微生物二次污染。
四、典型場景應用示例
? 市政污水處理超濾膜(PVDF材質):
物理清洗:每天運行結束后用產水正向沖洗15分鐘+氣水混合沖洗5分鐘;
化學清洗:每周用100ppm次氯酸鈉溶液循環清洗30分鐘,每3個月用0.1% NaOH溶液堿洗1小時。
? 工業廢水RO膜(聚酰胺):
物理清洗:每班次用原水正向沖洗10分鐘;
化學清洗:當脫鹽率下降5%時,先用2%檸檬酸(pH=3)酸洗45分鐘,再用1% NaOH+0.1% EDTA堿洗1小時,最后用亞硫酸鈉溶液保護。
通過規范操作步驟,可將膜通量恢復率提升至85%~95%,同時延長膜壽命至3~5年(未規范清洗的膜壽命通常僅1~2年)。在膜法集成技術中,物理清洗和化學清洗涉及設備操作及藥劑接觸,需嚴格遵守安全規范,避免人員傷害和設備損壞。以下是兩類清洗的安全注意事項及操作要點:
一、物理清洗安全事項
1. 高壓水流與氣壓操作
? 水壓控制:正向/反向沖洗時,壓力需≤0.3MPa(超過0.5MPa可能導致膜組件密封件破裂或膜絲斷裂),尤其反滲透膜嚴禁超壓沖洗(正常運行壓力0.8~1.5MPa,清洗壓力需低于運行壓力)。
? 氣水混合沖洗:壓縮空氣壓力需≤0.3MPa,且通氣時需緩慢升壓(每次升壓幅度≤0.1MPa),避免瞬間氣壓沖擊導致膜殼法蘭連接處泄漏或爆裂(曾有案例因氣壓驟升導致膜殼端蓋飛出)。
? 高壓設備防護:操作高壓泵時,需佩戴護目鏡,遠離管道接口及法蘭連接處(防止漏水噴射傷人),并在系統周邊設置警戒線。
2. 機械擦洗的設備安全
? 海綿球清洗:管式膜擦洗前,需確認膜管固定支架無松動,推入海綿球時速度≤1m/s,避免球體卡堵導致管內壓力驟升(卡堵時應立即停機,從膜管兩端拆卸法蘭取出球體)。
? 振動清洗(較少用):若使用機械振動裝置,需固定膜組件支架,振動頻率≤50Hz(高頻振動可能導致膜絲焊點脫落),每次振動時間≤5分鐘,防止膜組件疲勞損壞。
二、化學清洗安全事項
1. 藥劑接觸防護(核心風險)
? 酸堿藥劑:
? 配制2%檸檬酸(pH=3)或1% NaOH溶液時,需穿戴耐酸堿橡膠手套、護目鏡及防腐蝕圍裙,避免藥劑濺到皮膚或眼睛(若接觸,立即用大量清水沖洗15分鐘,并就醫)。
? 搬運藥劑桶時,需使用防泄漏托盤,樓梯或斜坡搬運時需兩人協作,防止藥劑桶傾倒(曾有案例因NaOH溶液泄漏導致地面腐蝕打滑,人員摔傷)。
? 氧化劑(次氯酸鈉/過硫酸鉀):
? 次氯酸鈉溶液(≤200ppm)需現配現用,避免與酸性物質混合(會產生有毒氯氣),儲存時需用避光塑料桶,遠離熱源(溫度>40℃時易分解產生氧氣,導致桶內壓力升高爆炸)。
? 過硫酸鉀屬于強氧化劑,禁止與有機物(如酒精、油污)接觸,配制時需用去離子水,操作人員需佩戴防塵面具(防止吸入粉塵刺激呼吸道)。
2. 系統化學清洗操作規范
? 藥劑溫度控制:清洗液溫度需≤35℃(聚酰胺RO膜在溫度>40℃時,堿洗會加速水解),加熱時需用循環水浴間接加熱,禁止直接用蒸汽通入藥劑桶(可能導致藥劑局部過熱分解)。
? pH監測與調節:
? 酸洗時實時監測pH,若pH>4需補加檸檬酸(確保pH=3~4),但補加時需停機并將清洗液排出10%~20%,避免藥劑濃度過高;
? 堿洗時若pH>12,需立即加入稀鹽酸中和(聚酰胺膜在pH>12時會脫層),并更換清洗液。
? 通風與廢氣處理:化學清洗需在通風良好的車間進行,若使用次氯酸鈉或鹽酸,需安裝局部排風裝置(防止揮發氣體刺激呼吸道),廢氣需通過堿液噴淋塔處理后排放。
3. 清洗后殘余藥劑處理
? 清洗結束后,沖洗水需檢測pH(6~9為合格)及余氯(≤0.1ppm),若pH超標,需用酸堿中和池處理;若余氯超標,需投加亞硫酸鈉還原(1ppm余氯需投加3.5ppm亞硫酸鈉),達標后才能排放(避免污染下水道或土壤)。
三、應急處理措施
1. 藥劑泄漏處理
? 酸堿泄漏:立即用沙土圍堵泄漏區域,用稀酸(堿)中和后,收集至專用廢液桶(如NaOH泄漏可用檸檬酸中和至pH=7);
? 次氯酸鈉泄漏:用硫代硫酸鈉粉末覆蓋(1kg次氯酸鈉需2kg硫代硫酸鈉),反應30分鐘后用清水沖洗地面。
2. 人員傷害應急處理
? 皮膚接觸:立即脫去污染衣物,用流動清水沖洗15分鐘(酸堿藥劑需延長至30分鐘),涂抹凡士林或中和藥膏;
? 眼睛接觸:撐開眼瞼,用生理鹽水沖洗20分鐘,就醫時攜帶藥劑MSDS(化學品安全技術說明書);
? 吸入藥劑蒸汽:迅速轉移至空氣新鮮處,保持呼吸道通暢,若呼吸困難需輸氧,直至救護車到達。
四、安全管理規范
? 培訓要求:操作人員需通過化學清洗安全培訓(每年復訓一次),考核合格后持證上崗,新員工需在資深人員監護下實習至少3次清洗操作;
? 設備檢查:每次清洗前檢查膜殼壓力表、安全閥(設定壓力≤0.4MPa)及管道法蘭墊片(老化墊片需更換),化學清洗泵需配備過載保護裝置;
? 安全預案:企業需制定《膜清洗安全應急預案》,明確泄漏、灼傷等事故的處置流程,并每季度組織應急演練。
通過嚴格執行上述安全措施,可將化學清洗事故發生率降低90%以上,同時避免因操作不當導致的膜組件永久性損傷(如酸堿腐蝕膜表面,氧化劑氧化膜材質)。
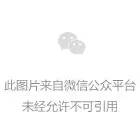
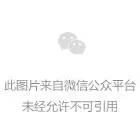
在物理清洗和化學清洗操作中,個人防護裝備(PPE)的選擇需根據操作風險和藥劑特性嚴格配備,以下是具體分類及裝備要求:
一、物理清洗個人防護裝備
1. 高壓水流/氣壓操作場景
? 頭部與面部防護:
? 護目鏡(防沖擊型,需符合ANSI Z87.1標準):防止高壓水流/水滴飛濺入眼(曾有案例因管道接口漏水,高壓水流沖擊導致角膜劃傷);
? 安全帽(可選):若在高處(>2米)操作高壓設備,需佩戴安全帽,防止頭部碰撞管道或支架。
? 身體防護:
? 防水工作服(PVC或橡膠材質):避免水流打濕衣物導致滑倒,同時隔離可能存在的微量藥劑殘留;
? 防滑鞋(橡膠底):操作地面若有水漬,需穿防滑鞋(摩擦系數≥0.5),防止滑倒摔傷。
? 手部防護:
? 防水手套(丁腈橡膠材質):耐磨損且防滑,抓取高壓管道或閥門時避免脫手(手套厚度需≥0.8mm)。
2. 機械擦洗(如海綿球清洗)場景
? 手部防護:耐磨帆布手套:防止搬運膜組件或擦洗工具時劃傷手部(膜殼法蘭邊緣可能存在毛刺);
? 眼部防護:普通防護眼鏡:防止機械部件拆卸時金屬碎屑飛濺。
二、化學清洗個人防護裝備(核心防護)
1. 酸堿藥劑操作(檸檬酸、NaOH等)
? 面部與眼部防護:
? 防腐蝕護目鏡(全包裹式):避免藥劑濺入眼睛(如配制10% NaOH溶液時,飛濺液滴可能導致角膜灼傷);
? 防酸堿面罩(可選):若藥劑揮發性強(如濃鹽酸),需佩戴面罩覆蓋全臉,防止蒸汽刺激面部皮膚。
? 身體防護:
? 防腐蝕圍裙(PVC材質,厚度≥1mm):覆蓋軀干,防止藥劑灑在衣物上滲透至皮膚;
? 防酸堿工作服(長袖長褲):選用聚乙烯涂層織物,接縫處需熱封處理(避免藥劑從針腳滲入);
? 防腐蝕靴(高腰橡膠靴):鞋幫高度≥15cm,防止藥劑潑濺到腳踝(曾有案例因NaOH溶液流入普通工作鞋,導致腳部灼傷)。
? 手部防護:
? 耐酸堿橡膠手套(氯丁橡膠或氟橡膠材質):手套長度需超過手腕10cm,且需定期檢查氣密性(可通過充氣法檢測是否漏氣)。
2. 氧化劑操作(次氯酸鈉、過硫酸鉀)
? 呼吸防護:
? 防毒面具(配酸性氣體濾毒罐):次氯酸鈉分解產生氯氣時,需佩戴防毒面具(濾毒罐型號需符合GB 2890-2009標準);
? 防塵口罩(N95級):操作過硫酸鉀粉末時,需佩戴防塵口罩,防止吸入氧化劑粉塵(可能刺激呼吸道黏膜)。
? 身體與手部防護:
? 防靜電工作服:氧化劑易與有機物反應,需穿防靜電材質衣物(避免靜電火花引燃周邊可燃物);
? 丁基橡膠手套:耐氧化劑腐蝕(過硫酸鉀會氧化普通橡膠手套,導致破損)。
3. 高溫清洗液操作(溫度>30℃)
? 身體防護:透氣型防燙圍裙:避免高溫清洗液(如35℃堿液)飛濺導致燙傷,圍裙需具有隔熱層(內層鋁箔反射熱量);
? 手部防護:耐高溫手套(硅膠材質,耐溫≥200℃):接觸加熱管道或藥劑桶時防止燙傷。
三、通用安全裝備及注意事項
1. 裝備穿戴規范
? 護目鏡需與面部緊密貼合(可通過吸氣測試是否有空氣漏入);
? 橡膠手套需在手腕處用膠帶密封,防止藥劑從袖口滲入;
? 防毒面具使用前需做密合性測試(捂住濾毒罐接口,用力吸氣,面罩應塌陷且無漏氣)。
2. 特殊場景補充裝備
? 有限空間作業(如進入膜池清洗):需額外配備:
? 自給式空氣呼吸器(SCBA):防止藥劑揮發氣體濃度過高導致窒息;
? 氣體檢測儀(檢測O?、Cl?、H?S濃度),O?含量需≥19.5%方可進入;
? 高空作業(>2米):需佩戴全身式安全帶,固定在承重≥1.5噸的錨點上。
四、裝備維護與更換標準
? 橡膠制品(手套、圍裙):若出現發粘、裂紋或硬化,需立即更換(化學藥劑會加速橡膠老化);
? 濾毒罐:次氯酸鈉作業中,若聞到氯氣味,需立即更換濾毒罐(通常使用時間≤8小時);
? 護目鏡:鏡片出現劃痕或模糊,需及時更換(影響視線可能導致操作失誤)。
通過精準配備PPE,可有效降低95%以上的藥劑接觸風險,同時避免因裝備缺失導致的職業健康傷害(如化學性眼灼傷、皮膚潰瘍等)。選擇物理清洗和化學清洗的防護裝備時,需從操作場景、藥劑特性、風險等級三方面綜合判斷,以下是具體選擇邏輯和實操指南:
一、基于清洗方式的核心風險識別
1. 物理清洗的主要風險
? 高壓水流/氣流:沖擊導致的身體挫傷(如高壓水槍反作用力致手腕扭傷)、飛濺物傷眼;
? 機械摩擦:膜組件金屬部件的毛刺劃傷、搬運時的碰撞擠壓。
2. 化學清洗的主要風險
? 酸堿腐蝕:10%以上濃度的檸檬酸可能導致皮膚紅腫,30% NaOH可瞬間灼傷角膜;
? 氧化損傷:次氯酸鈉分解的氯氣(濃度>1ppm時刺激呼吸道)、過硫酸鉀粉塵引發的皮膚過敏;
? 高溫灼傷:60℃以上堿液清洗時,飛濺液滴可能造成Ⅱ度燙傷。
二、防護裝備選擇的核心原則
1. 物理清洗裝備選擇邏輯
? 高壓作業場景:
? 必選:防沖擊護目鏡(抗120m/s高速粒子沖擊)+ 防水工作服(接縫處熱封處理)+ 防滑鞋(鞋底紋路深度≥3mm);
? 可選:高壓設備操作時若壓力>10MPa,需佩戴防沖擊耳罩(噪聲≥85dB時)。
? 機械擦洗場景:
? 重點防護手部和眼部:耐磨手套(手掌部位加厚至2mm)+ 普通防護眼鏡(透光率≥90%)。
2. 化學清洗裝備選擇邏輯
? 按藥劑類型分層防護:
藥劑類型 核心風險 必選裝備 升級裝備(高風險場景)
強酸(HCl) 液體飛濺、揮發氣體 全包裹防腐蝕護目鏡+PVC圍裙+氟橡膠手套 防酸蒸氣面罩+防腐蝕靴(靴底耐酸pH 1-14)
強堿(NaOH) 皮膚滲透、熱釋放 耐堿橡膠手套(厚度≥1.2mm)+防腐蝕工作服 耐高溫防堿靴(耐溫≥80℃)
氧化劑(NaClO) 氯氣泄漏、氧化腐蝕 防毒面具(配Cl?濾毒罐)+丁基橡膠手套 氯氣檢測儀(閾值設為0.5ppm)
? 按操作場景補充裝備:
? 有限空間清洗:需同時配備SCBA呼吸器(供氣流量≥30L/min)+ 防爆手電筒(ATEX認證);
? 高溫清洗(>50℃):手套需兼具耐化學性和隔熱性(如硅膠+玻璃纖維復合手套)。
三、實操中的快速決策流程
1. 第一步:判斷清洗類型
? 物理清洗:優先防護機械傷害和飛濺物 → 選防沖擊、防滑裝備;
? 化學清洗:先查藥劑MSDS(化學品安全說明書),明確以下參數:
? pH值(強酸強堿需全包裹防護);
? 揮發氣體種類(如Cl?需配專用濾毒罐);
? 閃點(若藥劑可燃,需穿防靜電服)。
2. 第二步:評估作業環境
? 空間密閉性:有限空間需增加呼吸防護(如正壓式呼吸器);
? 作業高度:>2米時必須配安全帶(雙鉤雙繩,沖擊載荷≤15kN);
? 環境溫度:冬季低溫作業時,橡膠手套需選耐低溫型號(-20℃仍保持柔韌性)。
3. 第三步:風險分級適配裝備
? 低風險(如清水沖洗):普通防護眼鏡+棉紗手套;
? 中風險(如1%檸檬酸清洗):防腐蝕護目鏡+丁腈手套+PVC圍裙;
? 高風險(如30%NaOH+次氯酸鈉聯合清洗):全包裹式防化服+自給式呼吸器+防化靴(需符合EN 13034液體致密性標準)。
四、典型錯誤案例與規避措施
1. 常見裝備選擇失誤
? 用普通乳膠手套操作濃鹽酸(30分鐘后手套溶脹破損) → 需換氟橡膠手套(耐酸度pH 0-14);
? 有限空間使用過濾式防毒面具(氧氣不足時導致窒息) → 必須用SCBA呼吸器(獨立供氣源)。
2. 規避措施
? 建立“藥劑-裝備”對應清單(示例):
藥劑名稱 濃度范圍 必選手套材質 護目鏡類型 呼吸防護
檸檬酸 <5% 丁腈橡膠 普通防濺護目鏡 無需(通風良好)
次氯酸鈉 5-10% 氯丁橡膠 全包裹防化護目鏡 防毒面具(Cl?濾毒罐)
? 作業前執行“雙人核查”:由安全員和操作工對照清單檢查裝備匹配性,重點確認:
? 手套材質與藥劑兼容性(可通過簡單溶脹測試:將手套邊角浸入藥劑10分鐘,觀察是否變形);
? 呼吸防護裝備的認證標準(如濾毒罐需標注GB 2890-2009)。
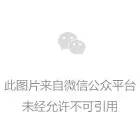
五、特殊場景的裝備升級方案
? 應急清洗場景:若突發膜污染需緊急化學清洗,現場無適配裝備時,可臨時用以下替代:
? 無防腐蝕圍裙 → 用聚乙烯塑料布包裹軀干(至少2層);
? 無耐酸堿手套 → 戴雙層丁腈手套(內層薄款+外層厚款),每30分鐘更換一次。
? 高毒藥劑作業:如使用甲醛(LC??=800ppm)清洗時,需升級為:
? 正壓式空氣呼吸器(供氣流量≥40L/min);
? 防化服需符合EN 14605液密性標準(接縫處 taped密封)。
通過“風險識別-參數匹配-環境評估-清單核查”四步法,可系統化降低裝備選擇失誤率,確保防護效果與作業安全性的最大化。
物理清洗和化學清洗在操作場景上的差異,主要由其技術原理、適用污染類型和設備特性決定,以下是具體對比:
一、核心差異:污染類型適配性
1. 物理清洗:適用于“可見性污染”
? 典型污染場景:
? 膜表面沉積的泥沙、金屬氧化物顆粒(如地下水處理中Fe3?形成的鐵銹層);
? 管道內殘留的纖維、毛發等機械雜質(如污水處理廠的MBR膜組件);
? 低黏度有機物附著(如食品工業廢水中的淀粉殘留)。
? 原理優勢:通過機械力直接剝離污染物,不改變污染物化學性質,適合處理“非黏性、非水溶性”雜質。
2. 化學清洗:適用于“化學性污染”
? 典型污染場景:
? 膜孔內的有機凝膠層(如石油化工廢水中的聚合物污染);
? 鈣鎂離子形成的碳酸鹽結垢(如海水淡化RO膜的CaCO?沉積);
? 生物膜滋生(如飲用水處理中細菌分泌的胞外聚合物EPS)。
? 原理優勢:利用化學藥劑(酸、堿、氧化劑等)與污染物發生中和、溶解、氧化反應,破壞其化學鍵,適合處理“黏性、水溶性差、生物性”污染。
二、操作環境與設備要求對比
1. 物理清洗:側重設備強度與空間開放性
? 典型場景特征:
? 高壓水清洗:需在開放空間作業(如室外膜組件清洗),設備壓力通常≥10MPa,配套高壓泵和耐高壓管路(爆破壓力≥工作壓力3倍);
? 機械擦洗:適用于可拆卸膜元件(如實驗室小型膜設備),需配備毛刷、海綿等工具,操作空間需滿足人工拆卸需求(高度≥1.8米,操作半徑≥0.5米);
? 反沖洗/氣擦洗:常用于在線清洗(如超濾膜系統),需膜設備自帶反洗管路,操作時需控制反洗流速(超濾反洗水速一般15-25m/h)。
2. 化學清洗:側重藥劑兼容性與密閉性
? 典型場景特征:
? 離線浸泡清洗:需專用清洗槽(材質為PP或PVC,耐酸堿腐蝕),如RO膜離線清洗時,需將膜元件放入容積為膜體積10倍的槽中,控制藥劑溫度30-40℃;
? 在線循環清洗:適用于大型膜系統(如市政污水處理廠),需配套清洗泵(流量≥設計產水量2倍)、保安過濾器(精度5μm)和pH調控裝置;
? 特殊場景:處理含氯藥劑時(如次氯酸鈉),設備需用316L不銹鋼材質(普通304鋼會被Cl?腐蝕),且作業空間需強制通風(氯氣濃度≤1ppm)。
三、時間與成本維度的場景差異
1. 物理清洗:適合“應急、低強度污染”場景
? 場景舉例:
? 膜系統運行通量下降10%時的日常維護(如每天一次反沖洗),單次操作時間10-15分鐘;
? 突發性泥沙污染(如暴雨后地表水濁度驟升),需立即用高壓水沖洗,避免污染物深層堵塞膜孔;
? 成本優勢:無需化學藥劑,主要成本為設備能耗(高壓水清洗功率約5-10kW/h)和人工,適合預算有限或環保要求高的場景(如飲用水處理)。
2. 化學清洗:適合“深度污染、周期性維護”場景
? 場景舉例:
? 膜通量下降30%以上的周期性清洗(如RO膜每3-6個月一次化學清洗),單次操作需4-8小時(包括浸泡、循環、沖洗步驟);
? 工業廢水處理中,膜表面形成生物垢后,需用NaOH+NaClO聯合清洗(pH控制12-13,氧化還原電位ORP≥600mV);
? 成本考量:藥劑費用占比高(如檸檬酸約5元/kg,次氯酸鈉約2元/kg),且需配套廢水處理設施(清洗廢液pH需調節至6-9才能排放),適合高附加值水處理場景(如電子級超純水制備)。
四、特殊行業的場景適配案例
1. 物理清洗典型行業
? 食品飲料行業:牛奶濃縮超濾膜的每日CIP(在線清洗),用清水+溫水反沖洗,避免化學藥劑殘留影響產品風味;
? 市政水處理:預處理階段的膜過濾裝置,定期用空氣擦洗(氣速100-150m/h)去除懸浮顆粒物,降低后續化學清洗頻率。
2. 化學清洗典型行業
? 石油化工:煉化廢水處理中的RO膜,需用10%鹽酸+0.5%EDTA清洗鈣鎂結垢,每年2-3次;
? 制藥行業:注射用水制備系統的UF膜,需用3%H?O?+0.1%NaOH進行滅菌清洗,每月一次,確保微生物指標符合USP標準。
五、組合清洗場景:物理+化學協同應用
? 適用場景:重度污染或復雜污染物(如既有結垢又有生物膜),單一方法效率低時;
? 操作流程舉例:
1. 先物理清洗:用高壓水(壓力15MPa)沖洗膜表面可見雜質;
2. 再化學清洗:用2%檸檬酸(pH 3)溶解無機垢,后用1000ppm NaClO氧化生物膜;
? 行業案例:海水淡化SWRO膜,每半年進行“氣擦洗+酸洗+堿洗”組合清洗,可將膜通量恢復率從單一化學清洗的80%提升至95%以上。
通過污染類型、設備條件、成本效率和行業特性四個維度的判斷,可精準匹配物理或化學清洗的適用場景,最大化清洗效率并降低運維成本。物理清洗和化學清洗的操作流程因原理差異呈現顯著不同,以下從流程框架、關鍵步驟及典型場景舉例展開對比:
一、流程框架:物理側重“機械作用循環”,化學側重“藥劑反應控制”
1. 物理清洗:流程簡潔,以“機械力施加”為核心
? 典型流程(以高壓水清洗為例):
1. 預處理:拆除待清洗設備(如膜組件),檢查表面可見雜質;
2. 機械作業:用高壓水槍(壓力10-50MPa)從不同角度噴射污染物,持續至表面無明顯殘留;
3. 沖洗收尾:用清水沖洗設備表面,確認無顆粒殘留后組裝復原。
2. 化學清洗:流程復雜,需“藥劑配比-反應-中和”全流程控制
? 典型流程(以RO膜酸洗為例):
1. 配藥:在清洗槽中配制2%檸檬酸溶液(pH調至3.0),升溫至35℃;
2. 循環清洗:用清洗泵將藥劑循環通過膜系統,流量為設計產水量2倍,持續60分鐘;
3. 浸泡反應:停止循環,讓藥劑浸泡膜元件30分鐘溶解鈣鎂垢;
4. 中和沖洗:用清水沖洗至出水pH=7,若藥劑含強酸,需用NaOH溶液中和廢液至pH 6-9。
二、關鍵步驟差異:物理重“力度與角度”,化學重“濃度與時間”
1. 物理清洗核心操作要點
? 高壓水清洗:
? 噴頭與清洗面距離控制在10-30cm,移動速度5-10cm/s,避免局部沖刷過度導致設備損傷;
? 對管道內壁清洗時,需用旋轉噴頭(轉速100-200rpm)確保360°覆蓋。
? 反沖洗/氣擦洗:
? 超濾膜反洗水速需達15-25m/h,氣擦洗時氣速控制100-150m/h,持續5-10分鐘,通過流體剪切力剝離膜表面污染物。
2. 化學清洗核心操作要點
? 藥劑配制:
? 酸洗劑(如鹽酸)需緩慢倒入水中(防止酸液飛濺),同時攪拌散熱,避免局部過熱;
? 氧化性藥劑(如次氯酸鈉)需現配現用,避免久置失效(有效氯含量每小時下降5%)。
? 反應控制:
? 清洗溫度通??刂?0-40℃(溫度每升高10℃,反應速率提升2倍),但需注意膜材質耐受極限(如PVDF膜耐溫≤50℃);
? 循環過程中需實時監測藥劑pH(波動超過±0.5需補加藥劑),確保反應持續有效。
三、流程耗時與頻次:物理適合“高頻短時間”,化學適合“低頻長時間”
1. 物理清洗
? 操作耗時:單次10-30分鐘(如膜系統日常反沖洗),可在線進行,不中斷生產;
? 適用場景:污染程度輕、需頻繁維護的場景(如食品廠每日生產后設備沖洗)。
2. 化學清洗
? 操作耗時:單次4-8小時(含配藥、循環、浸泡、沖洗),需離線作業,中斷系統運行;
? 觸發條件:當膜通量下降30%以上或跨膜壓差(TMP)上升50%時啟動,通常每3-6個月一次。
四、典型行業流程對比
1. 物理清洗案例:市政污水處理膜池清洗
? 流程:
1. 開啟膜池底部曝氣裝置(氣速150m/h),進行30分鐘氣擦洗,剝離膜絲表面污泥;
2. 切換至反沖洗泵,用處理后清水以20m/h流速反洗15分鐘;
3. 恢復正常過濾,整個流程在在線狀態下完成,不影響出水水質。
2. 化學清洗案例:電廠鍋爐反滲透膜清洗
? 流程:
1. 離線拆卸膜元件,放入PP材質清洗槽,配制0.1%NaOH+0.5%NaClO混合液(pH 12);
2. 循環清洗2小時(溫度35℃,流量50m3/h),氧化分解生物膜;
3. 排盡堿液,換用1%檸檬酸溶液(pH 4)循環1小時溶解鈣垢;
4. 用RO產水沖洗至出水電導率≤10μS/cm,耗時總計約6小時。
五、組合流程:物理+化學協同操作步驟
? 適用場景:重度污染(如既有結垢又有有機物污染)
? 流程示例(以海水淡化膜清洗為例):
1. 物理預清洗:用高壓水(20MPa)沖洗膜殼內壁,去除大顆粒泥沙;
2. 化學清洗1(酸洗):0.5%鹽酸溶液循環清洗,溶解CaCO?結垢,持續90分鐘;
3. 化學清洗2(堿洗):1%NaOH+1000ppm NaClO溶液浸泡2小時,降解有機物和生物膜;
4. 物理收尾:用海水淡化產水高壓沖洗(壓力1.0MPa),確保藥劑殘留≤0.1ppm。
綜上,物理清洗流程以“機械力快速作用”為核心,適合表面污染的高頻維護;化學清洗依賴“藥劑反應深度清潔”,需嚴格控制藥劑參數,適用于周期性深度維護,兩者在流程設計上的差異本質是“效率”與“效果”的權衡。選擇物理清洗和化學清洗的清洗劑時,需結合污染物類型、設備材質、清洗場景等核心因素,遵循“針對性溶解/剝離”原則。以下從污染物分析、藥劑特性、安全限制三方面展開說明:
一、根據污染物類型匹配清洗劑功能
1. 物理清洗:無化學藥劑,依賴介質物理特性
? 常用介質及適用場景:
? 高壓水:適用于水溶性顆粒(泥沙、粉塵)、輕度油污,通過沖擊力剝離表面污染物(如換熱器外壁沖洗);
? 干冰/噴砂:干冰升華吸熱使污垢收縮脫落,適用于橡膠、塑料等敏感材質(如食品設備殘留清洗);噴砂(石英砂/玻璃珠)通過高速撞擊去除頑固銹層(如管道內壁除銹),但需注意設備耐磨損性。
2. 化學清洗:按污染物化學性質選藥劑類型
污染物類型 典型案例 適用化學清洗劑 作用原理
無機垢 鈣鎂碳酸鹽、硫酸鹽 鹽酸、檸檬酸、氨基磺酸 酸堿反應生成可溶性鹽
金屬氧化物 鐵銹、銅綠 硝酸(配合緩蝕劑)、氫氟酸 氧化還原反應溶解金屬氧化物
有機物/生物膜 油脂、蛋白質、藻類 氫氧化鈉(堿洗)、次氯酸鈉 皂化反應(油脂)、氧化分解(生物膜)
聚合物殘留 樹脂、油漆 丙酮、甲苯(需注意揮發性) 相似相溶原理溶解高分子化合物
二、考慮設備材質與藥劑兼容性
1. 物理清洗:介質硬度需匹配材質耐蝕性
? 示例:
? 鋁合金設備禁用噴砂(砂粒硬度>鋁合金,易造成劃痕),改用高壓水(壓力≤10MPa)或干冰清洗;
? 玻璃材質設備避免使用顆粒介質,以防破裂,可選用低壓水+軟毛刷清洗。
2. 化學清洗:藥劑腐蝕性與材質耐受范圍
? 常見材質禁忌:
? 不銹鋼(304/316):禁用含氯離子藥劑(如鹽酸),易引發應力腐蝕,可選用檸檬酸(濃度≤3%);
? 銅合金:避免使用氨類藥劑(生成銅氨絡離子),優先選氨基磺酸清洗銅銹;
? 塑料(PVC/PP):耐酸不耐強氧化劑,如次氯酸鈉濃度需<0.1%,以防老化開裂。
三、兼顧清洗效率與安全環保要求
1. 效率導向:根據污染程度選藥劑濃度與配方
? 輕度污染:低濃度藥劑(如1%檸檬酸)配合物理沖洗(如反沖洗),縮短清洗時間;
? 重度污染:復配藥劑(如“檸檬酸+表面活性劑”)增強滲透力,必要時升溫(30-50℃)提升反應速率。
2. 安全環保限制
? 毒性與揮發性:
? 化學清洗避免使用氰化物、氟化物(如氫氟酸需嚴格管控),優先選可生物降解藥劑(如聚天冬氨酸類螯合劑);
? 揮發性有機物(如甲醇)需在密閉系統中使用,并配備廢氣處理裝置。
? 廢液處理成本:
? 強酸強堿藥劑(pH<2或>12)需中和后排放,選藥劑時優先考慮低濃度、易中和類型(如檸檬酸廢液可用碳酸鈣中和)。
四、典型場景清洗劑選擇示例
1. 工業鍋爐管道清洗
? 污染物:碳酸鈣為主的水垢+鐵銹
? 方案:
? 化學清洗:2%氨基磺酸(配0.5%緩蝕劑),避免鹽酸對碳鋼的腐蝕;
? 物理輔助:清洗后用高壓水(15MPa)沖洗殘留藥劑,防止結晶。
2. 食品廠灌裝線清洗
? 污染物:蛋白質、油脂殘留
? 方案:
? 化學清洗:1-2%氫氧化鈉溶液(60℃循環),皂化油脂并溶解蛋白質;
? 安全要求:藥劑需符合FDA食品接觸標準(如USP級氫氧化鈉),清洗后用飲用水沖洗至TOC<5ppm。
3. 半導體晶圓清洗
? 污染物:金屬離子、光刻膠殘留
? 方案:
? 化學清洗:超純水+臭氧(氧化分解有機物),配合稀釋氫氟酸(0.5%)去除氧化物;
? 材質兼容:設備需用PVDF或石英材質,避免金屬離子污染。
五、組合清洗策略:物理與化學協同增效
? 先物理后化學:
? 場景:設備表面有大顆粒雜質+頑固垢層(如換熱器管束)
? 步驟:高壓水沖洗去除顆?!?%硝酸(配緩蝕劑)溶解銹層,減少藥劑用量。
? 化學溶解+物理剝離:
? 場景:生物膜污染的水處理膜
? 步驟:次氯酸鈉(500ppm)氧化生物膜→氣擦洗(氣速120m/h)剝離脫落物質,提升清洗效率。
總結選擇邏輯
1. 第一步:分析污染物成分(無機/有機/生物),確定化學藥劑類型或物理介質;
2. 第二步:核查設備材質,排除禁忌藥劑(如不銹鋼禁含氯藥劑);
3. 第三步:評估清洗效率與環保成本,優先低毒、易處理藥劑;
4. 第四步:重度污染或復雜場景采用“物理+化學”組合方案,平衡效果與安全性。
如果您有污水項目資源,可跟我聯系。提供污水廢氣項目投資、設計、設備(配件)、施工安裝、運維等服務。環境治理工程師18823239363王勤、微信同號。佛山市德龍信環保設備有限公司的產品和服務具有以下優勢:
1. 專業技術:公司可能擁有專業的環保技術團隊,具備豐富的經驗和專業知識,能夠提供高質量的環保設備和解決方案。
2. 產品質量:注重產品質量,可能采用先進的技術和優質的材料,生產出可靠、高效的環保設備,滿足客戶的需求。
3. 多樣化產品:公司可能提供多樣化的環保設備,如污水處理設備、廢氣處理設備、噪聲控制設備等,以滿足不同領域和客戶的需求。
4. 定制化服務:能夠根據客戶的具體要求和環境特點,提供定制化的環保解決方案,確保方案的針對性和有效性。
5. 售后服務:可能提供良好的售后服務,包括設備安裝、調試、培訓、維護等,以確保設備的正常運行和客戶的滿意度。
6. 技術創新:注重技術創新,不斷研發和推出新的環保技術和產品,以適應市場的變化和客戶的需求。
7. 市場口碑:在行業中可能擁有良好的口碑和聲譽,得到客戶的認可和信賴,這有助于吸引更多的客戶和業務。
8. 環保意識:公司可能注重環保理念的推廣和實踐,積極參與環保事業,為社會和環境做出貢獻。
【德龍信品牌】環境污染治理工程建設二十年老企業、不斷創新發展為全球企業提供專業的解決方案及技術咨詢產品設備出口等服務。歡迎大家咨詢合作??共同發展、共創美好家園。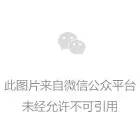